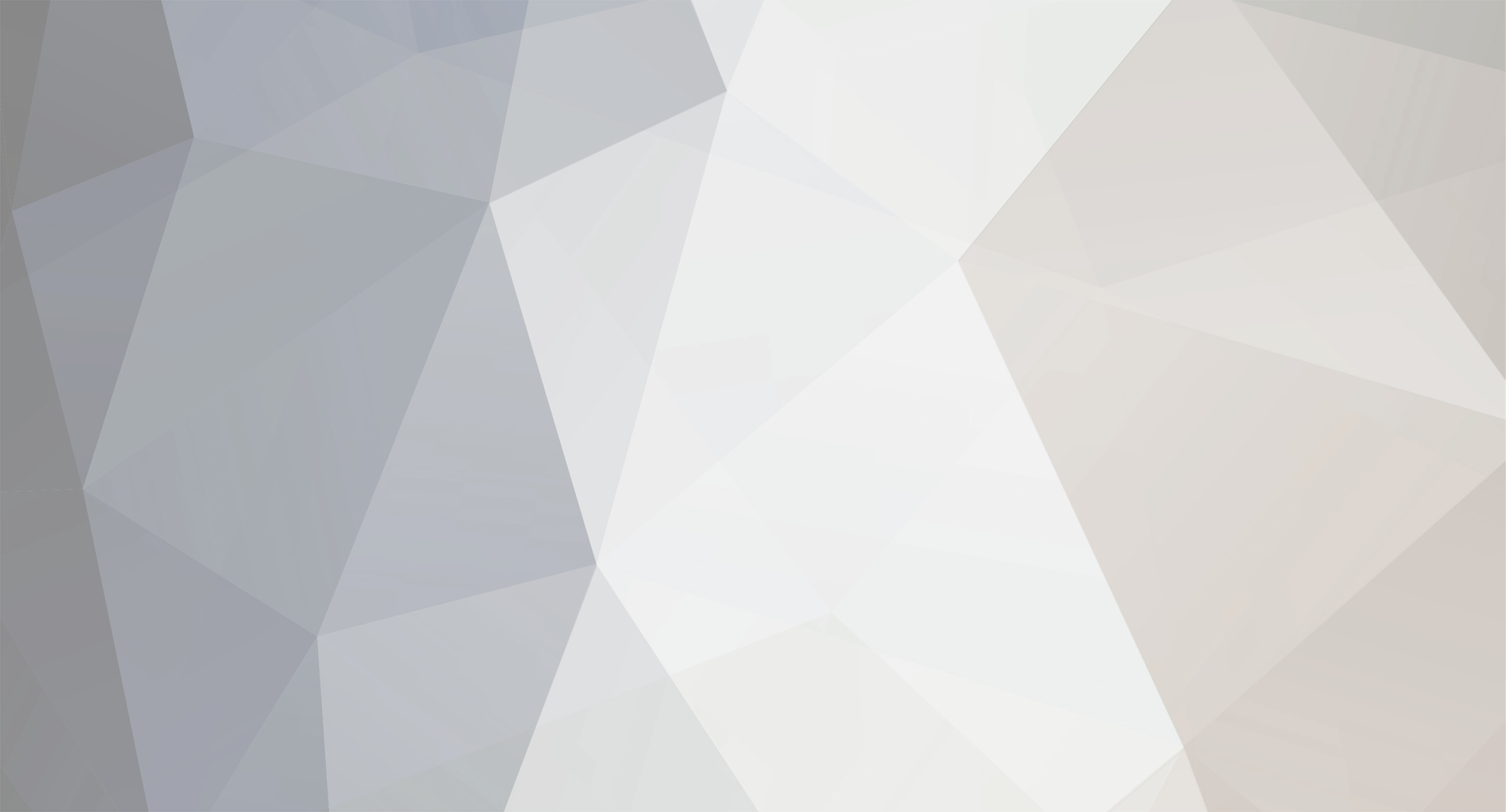
David Hall 9
Members-
Posts
363 -
Joined
-
Last visited
Content Type
Profiles
Forums
Blogs
Gallery
Calendar
Downloads
Everything posted by David Hall 9
-
Things that have dropped off in flight
David Hall 9 replied to Chris Walby's topic in All Things Model Flying
During launch on my first or second F5J comp, my E glider threw a blade off my (cheap and nasty) folding prop. The motor and bulkhead instantly parted with the airframe, leaving the battery in place (good old Velcro!). The glider came down (with no input from me) like an autumn leaf and suffered no extra damage. The motor was much further away than I had imagined, but was found. -
Posted by Peter Millward 1 on 10/06/2020 22:01:04: Thumper 3536/08 and a XP2 40A and a 3S Overlander 2200Mah lipo I presume all these should work together. They "should" be fine together... as you have made no attempt to (deliberately) run or load the motor. So it is a case of the BEC powering the Rx/servo set. Sadly, there are instances of defective parts, new or not, that can catch you out... A little more of my education came when testing a few cheap receivers on the bench... A cheap "no name" ESC to power the Rx and 1,2 or 3 servos fitted. The power "glitches" or failing BEC was only seen on one of the two receivers in combination with one ESC. Bearing in mind that if this was a load issue, I could expect a very much worse case when in flight. I concluded that it was probably a noisy/poor BEC in combination with a cheap receiver with poor supply noise immunity. Rather than sort out working combinations, I binned the lot. I suggest that you apply a similar approach and bin the ESC, or at least bag it, marked suspect. Save yourself one or more models.
-
Posted by Peter Millward 1 on 10/06/2020 19:17:31: No the servos either lock up or move without any imput from Tx I had an ESC with BEC on which the output collapsed when the three servos connected were moved (or twitched). It caused the BEC output to shut off then restart. This made the servos twitch around continuously once they were started off. I suspect that your ESC/BEC is faulty. You could confirm by powering from some other source (the second ESC) with the red power lead from the suspect BEC disconnected... Or try one servo, then two etc.... it looks like it could be a power brownout thing.... You don't need the motor to be connected to test this. Edited By David Hall 9 on 10/06/2020 19:38:02
-
Do the servos continue to work as you would expect them to once the motor is misbehaving?
-
Posted by Steve J on 10/06/2020 10:03:58: Posted by Lima Hotel Foxtrot on 10/06/2020 09:47:09: If you buy cheap, you'll buy twice. Not necessarily, but you have to know what you are doing and be prepared to write off the purchase. I've bought lots of stuff from banggood, mostly small orders of electronic bits, and I am happy with what arrived. This is my experience too. Small items have arrived (one in twenty-odd orders did not arrive and was refunded). In general, anything that I might want to return, I buy locally. Items from BG have been generally very good but if not of the quality I expect, I just write them off. I also try to keep my orders below £15 to ensure that I don't get caught for duty and tax. Edited By David Hall 9 on 10/06/2020 13:30:49
-
Posted by I_AM_MARKEVANS on 07/06/2020 12:09:01:...................................The unwanted servo movement bug present in V1 is very rare, personally I am still flying on V1 and have no intention of upgrading. I have seen enough issues over on RCG with them trying to iron out all the bugs and issues with the V2 firmware in the rx's like the G-RX8 and even the RX4&6R that I feel its more stable on V1 with the known bug than it is on V2. ............................................... What is the nature of the bug on V1? ... some issues that apply particularly to, say, multirotors or helis might never be an issue for fixed wing. I guess that I don't need to upgrade to fix a bug in something that I don't use.
-
I understand, it's something that I read recently too. My receivers' firmware is as it was when they were bought. I also read that there is no way to check what is loaded. You can re-flash to a known issue level, if it's the latest, you may also have to upgrade your Tx firmware. Have you experienced glitches on your D16 receivers?
-
I run my Qx7 on OpenTx 2.2.1 and my recently acquired X9D on 2.2.4. The X9D is on 2.2.4 because couldn't find a way to load it with 2.2.1 to match my Q7x. It is not problem though, they seem to be fully compatible and fairly complex model configurations were transferred (via Companion) without any issues. My Receivers are D8 or LBT D16 versions and all work perfectly well on either Tx. I can't find a problem with any of the system that would make me want to upgrade. I am concerned that any upgrade to 2.3.x might cause a need to adapt my many model configurations. There are some aspects of telemetry that don't quite suit me, but I understand that these points remain the same in later versions. In the end...it all works very well for my use, upgrading for no reason other than to have the latest (for which changes might not effect fixed wing flying), can cause some rework to be needed. Edited By David Hall 9 on 07/06/2020 10:45:01 Edited By David Hall 9 on 07/06/2020 10:47:51
-
I re-started with the inexpensive FS -i6 and 6ch receivers when I came back to the hobby. I found the set to be a great performer, although the Tx size can look a bit small. I have now moved to FRSKY for the endless mixing possibilities that are possible and needed for my thermal gliders, and can still use my FLYSKY receivers. For models, if you are not keen to build from a kit, maybe look at ARTF models (assemble and add your own radio/servos/motor). I like the Topmodels gliders as sold via T9 Hobbies.
-
I tried unsuccessfully to find info/video of the first stage landing... anyone seen a video of the landing?
-
Motor thrust alignment Junior 60
David Hall 9 replied to Skippers Walker's topic in General Electric Flight Chat
My recently finished (&flown) Junior 60 is my first "Vintage" model. I don't know what kit it came from, it was powered by a big brushed motor with an equally big belt drive gear system. The motor appeared to be mounted on bearers that had very little or no down thrust. I replaced the power system with a 3730 1000kv motor with the intention of 2S operation. It was flown initially on 3S with the throttle wound down to 50% and was still overpowered. My F5J gliders all have a simple mix on the throttle to include a throttle to (down) elevator mix, adjustable on a Tx trim. I copied the mix to my J60 config. Without the mix, the Junior 60 would loop if left to itself during a high power run. With the mix added and adjusted, the climb is as I like it and the glide is spot-on... it all works well for gentle flying. Incidentally, I still would like 2S operation. The same motor on 2S with a 13x7 prop on my E-glider sounds perfect, a nice calm whir. I would need higher capacity packs for the J60 but adding to my present battery collection is not a good idea. I measured the input power at around 200w and have now replaced the motor with a 2826/950kv and 11x6 prop (plus a little extra weight in the nose). I have yet to fly this. -
Thanks for the pointer..... the German manual was useful. The motor mount plate appears to be simply tightened on a screw thread. If (big IF) no thread lock was used on it, I should be able to disassemble it. I'll need a new pinion gear I guess, and some Loctite to fix it on the shaft. Any parts suppliers in the UK?
-
I had once considered how i would set up a four engine model for electric. The problems for me were, where to put the battery and how to control the motors. The battery position was easier, I guess. One battery for each side. The motor control, without being too techy, was to put the inner and outer motor pairs onto their own channel and to apply a curve to the outer motors to delay their power-up slightly behind the inners. Never got past any planning and now other projects got in the way.
-
Use of SBUS/PPM converters in a wing.
David Hall 9 replied to David Hall 9's topic in General Radio Discussion
Thanks for the warning about possible problems using analogue servos. I quite like to use analogue at most, but not all control surfaces, so tend to end up with a mix. Without a scope or such, I guess that a stalled analogue servo making the "normal" (old) buzzing noise around 50hz will be receiving a suitable frame rate, but if it buzzes with a significantly higher note, there's a problem? EDIT: just noticed a "Hz" position on my multimeter... The meter shows 50Hz for the output from my iA10B FLYSKY Rx... handy... Edited By David Hall 9 on 07/05/2020 12:34:52 -
I have just completed my "Inside F5J" glider and wired the six servos in the wing, along with the connection into the fuselage. I had read of others planning to use an SBUS/PPM output from their Rx to drive a converter in the wing (or attached to the wing). This would allow the wing-fus connection to be a single three pin servo connector. It's too late for my six servo wing which is now ready, but my future (probably) four servo wings could use this setup. Four/eight channel converters are readily available and quite cheap. I can run the inexpensive FLYSKY iA6B (6CH Rx) from my Taranis Tx via the multimodule, and the later firmware for this Rx supports 8CH SBUS. I can wire the three channels to the Thr/Ele/Rud as normal using the first three channels, then pick up channels 5 to 8 inside the wing on the converter via SBUS. I'm sure that SBUS/PPM is reliable, has anyone had experience with these cheap converters? Edited By David Hall 9 on 07/05/2020 10:04:24
-
Varying wing section info?
David Hall 9 replied to David Hall 9's topic in Gliders and Gliding - General Discussion
Thank you for the very detailed explanation Peter Jenkins. I guess then, that the value of a specific varying section is arguably overkill on a model, but especially on a model wing of film covered open ribbed structure. The ribs might be accurate, but sagging film section between the ribs must be difficult to design to a known section. Edited By David Hall 9 on 02/05/2020 11:14:55 -
Lots of adapters available... start with a search like this....
-
It's good stuff, if a little messy at times. Be aware that as it expands in a gap, it can push parts apart, so clamp/pin things to be glued.
-
Posted by Bob Cotsford on 01/05/2020 18:24:48: I spotted these and thought that for £35 it would occupy a few hours. The kit comes as a mixture of laser cut poplar ply and balsa sheets. At 300mm wingspan it's intended for small multirotor motors around 2000-2500kv running on 3 or 4S packs up to 1000 mAh and two micro servos. I have a 180W BL-2208/12 motor, 20A esc ................................ Is it 300mm span?... doesn't give the span on the website... looks bigger.
-
As if to underline the effect of QA, I've just found another Hobbywing 3A UBEC, of the same type as the one that I tested. It's like a different device, the voltage regulation is much poorer than the first... it's a game of chance at the budget end ..
-
When I came back to RC, I bought a bunch of no-name ESCs and a few Chinese DSMX compatible receivers. They all looked fine. I set them up on the bench and added servos. When I got to three servos, one twitch on the stick set off a shutdown that cycled on and off. Two of the three Rx's did this. A good Rx was fine. Now I test more often. But my test does show that my current supply need is probably lower than I thought. I use the ZTW ESC in several planes and have no problems. If the one tested is a representative sample (low shut-off current), then I use less than I thought I needed.
-
My setup on a Qx7 works well, although I haven't used crow braking yet It is configured, but I may not need it as flaps at around 80 degrees down brake very well on my lighter gliders. I take the flap input (switch/stick etc) and put it on a separate unused channel. Flap is the same as spoiler, but in the opposite direction. I add flap to the flaps (some have aileron added), just add CH whatever, + 0r - weight. Similar for the aileron, add flap but in the opposite direction. Edited By David Hall 9 on 28/04/2020 17:12:41
-
I have a small collection of BECs that were/are destined for use in my smaller F5J and sports gliders. I had found that the current output of the average ESC/BEC combo tends to be on the low side. For a 6 digital servo setup, I would choose something more like 4A min. For my latest 8 servo glider, a higher output is recommended in order to avoid supply collapse and brownout. At the same time, I've started using opto ESCs, which can be remarkably small and light. I just need to find a separate BEC. I had a few small ones in hand and had bought a 4A and a 5A version for my plane. As I recently bought a variable discharge load, I have all the kit I need to actually test my BECs, so I set up on my bench and ran all the BECs I had. There were some surprises, but first let me say that QC, as always, plays a part in the performance we see.... you might see different performance. I had set out a few tests for all the BECs, using a 3S battery. First to see at what current the output collapsed (increasing quickly). Second, measure the voltage at 67% then 100% of the rated output and see how fast they heated up. My ZTW Beatles 30A ESC output collapsed at 3A/4.1v. It gave 5.1v off load, 4.1v at 2A and at 3A (constant) it melted the heatshrink covering quite quickly. Test aborted. Turnigy 5A 8-26V input SBEC. 5.3v no load, O/P collapsed at 4.1A. At 67%/5.0v it was getting too hot quickly. Test aborted. Hobbyking 4A no brand SBEC. Output collapsed at 3.5A. To cut out more wordy detail, the KingKong and Hobbywing 3A SBEC (UBEC) did very well, both maintained an output over their rated 3A. The HW maintained 5.4-5.1v right up to 3.5A when the output shut off (collapsed) and was the coolest at 67% output. The King Kong didn't keep such a good regulation but managed a transient output of 4.3A. The real surprise was the tiny FPV bluesky UBEC 5v. This sold as a 3A device. I tested two. The best had excellent regulation, 5.3v, down to 5.1v at shutoff at over 4A. Managed 5.2v @2A, 5.2v @3A (getting warm), Held 2A fairly well, just getting too hot to hold after ~1.5min. So... my fav ESC (this example) output is lower than rated, but that might be max transient output, not constant. The higher output SBEC of 4A and 5A are poor, and the super cheapies were very good in this test.... just what kind of noise is output on the supply is something else, I guess. My tests were based on my need, to supply rather high transient output current whilst maintaining a reasonable steady output. I think that is shows how the spec can vary almost wildly and probably be effected by QA issues. Edited By David Hall 9 on 28/04/2020 17:05:01