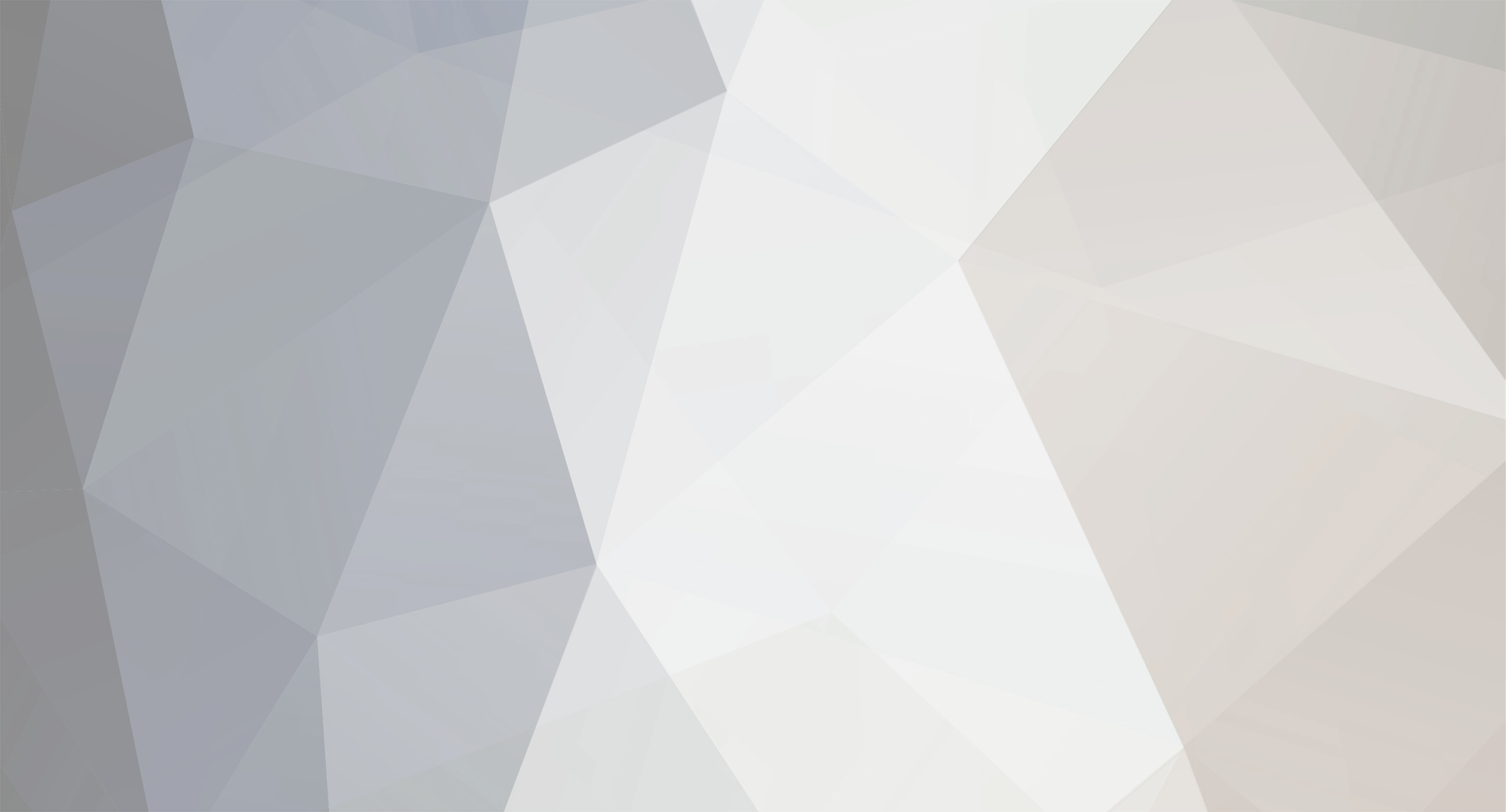
Bob Smitham
Members-
Posts
143 -
Joined
-
Last visited
Recent Profile Visitors
The recent visitors block is disabled and is not being shown to other users.
Bob Smitham's Achievements
2
Reputation
-
Give this thread by FylinFinn a look over if you already have a 3D printer the build comes in at around £100. A lot of playing around with bits of software is required but within a week I was cutting ply and balsa.But being printer owners I'm sure you are familiar with that.
-
I did start off looking for an off cut of wood Nigel.But the length of aluminium sat in the corner and the pub being a fading memory conspired to send me off on this tangent. A few more tricks on Fusion 360 learned along the way which is always handy.
-
I will check them KC thanks for the link. The "fuse on tube" sounds interesting extra slim for some idea stealing .The only commercial ones I could see were the peg board verity.
-
A little further down the road with this side project.A few varying clamp designs fitted to the rail and a few improvements being made as I test the latest components.This work is mostly extending the clamp heights.The side clamps are now fastened with bolts(sourcing some wing nuts for theses). My requirement for a space saving mobile build jig are getting there .The extrusion rails give a good centre line for alignment and a flat surface for reference to T squares,spirit levels and the like.The ability to pick up a build in progress and turn it around for access ,or store it away was my principle aim. It can be placed on a shelf or hung from a wall when the precious bench space is needed for other work.And the addition of being able to hold it like a rifle and view the build from a down the "gun sights" angle is a bonus I didn't think of.I can now leave the jig hung up and set the CNC up in its place to carry on cutting the plan.No doubt as the build progresses the design will change.
-
I agree with your points kc.It's mostly easing lockdown boredom this project.Creating a overly complicated solution to a simple problem.The apocryphal story of the one million dollar development budget NASA space zero G pen.And the Soviets using a pencil springs to mind. But the alternative (checks TV listings) is Loose women.
-
It's the SLEC style width clamps are what I'm working on now.The only thing slowing me down is the print times.A reasonable amount of internal structure is needed for strength.This simple but clever sliding clamp found thingyverse takes two and a half hours.A neat design with an eccentric cam for locking it in place.But adapting this design for a 2040 section extrusion profile will push my limited CAD knowledge.
-
In preparation for lock downs four too five and to utilise Flying Flynn's laser CNC design. I have once again probably bitten off more than I can chew with complicated monocoque build that's going to require a jig.A magnetic or large board jig will swallow up the last few square inches in my tiny shed/workshop.So I need something small and mobile that I can put on a shelf or hang from the wall at various build stages when my bench space is required for other tasks. . I was on the look out for a nice straight piece of 6"1 plank to use .But that would be far too easy for a masochist such as my self.So I've set about on a doomed mission to reinvent the wheel.A length of 2040 aluminium extrusion with 3D printed adjustable sliding attachments. Hours of Fusion 360 doodles and failed prints later it's starting to get somewhere. Only after printing and actually attempting to use the adjustable bit's and pieces have the short falls come to light.Which is parr for the course I find with any design I attempt.The yawning chasm between my ideas and the practicalities of the real world. The two clamps in the centre with 3D printed threads work surprisingly well and fastened nice and snug on printed 12mm 1.25 threads.The printed threads were slowly worked through with a little vaseline in the manner of tapping a thread.I was intending to sink a bolt into the bases and use steel bolts.But I found these leave indentations in the soft Ally. How ever a taller vice faces will be added to V15.The contraption on the left is a height adjustable clamp holder. I'm still undecided as to whether this is of any practical use.The feet I stole from Flying Flynn's CNC STL's? It is all work in progress what with this being my first build from plan.And I expect all the clamps and gubbings will change with each stage of the build.The side supports being the part of the plan that won't get a second outing on the print bed.I was guilty of over thinking in that department.Using a notched rail to adjust width and a lack of height on the clamp making its uses limited. . The obvious way for these side guides/clamps to be fitted is a slot and a simple nut n bolt.Blindingly obvious after struggling with CAD and a six hour print. So before embarking on any more wasted CAD and printing time do any jig users have any suggestions as to what may help turn this daft idea into something usable?I realise a plan over a steel build plate is probably the better option.I will have to measure the distances for the remaining tail sections but hopefully all will provide a straight base to build from for my first foray into planking a fuselage.
-
Really enjoying following this build Tim.But you have convinced me I'm a build or two away from attempting this kit.The DB spit was on my potential next build list. But the information and pictures are continuing my education in the dark arts.
-
Posted by Peter Miller on 19/01/2021 15:01:31: I wonder does anyone ever forget that first successful flight. I know that I can still remember mine. I remember the complete scene,the weather and that flight. I had built quite a few rubber powered models which converted themselves into instant scrap. This was in 1953 when I was living in the Argentine. I built a cabin Wakefield called the Cardinal. The kit was bought at the only real model shop in Buenos Aires called Maipu 309 which also happened to be its address. I took the model up onto a huge open grass field. I can still see the scene with a house among trees up a slight rise about 300 yards away. I wound the model up and launched it. IT FLEW. It climbed away and circled round for about a minute an then landed quite near me. Absolute JOY!!! For the second flight I went with my mother and the dogs to a large area of scrub and grass where there were usually cattle grazing...no fences. This time I was going to stretch wind the motor. With mother holding the model I stretched the motor out and started winding with the hand drill with hook in the chuck. The rear motor peg pulled out and suddenly I had about 8 ounces of rubber with assorted balsa bits being chewed up in it while my mother was left holding four longerons and a wing and a tail. Again.I cannot forget that. If anyone has a plan of that Cardinal Wakefield I would give an awful lot for a copy. Edited By Peter Miller on 19/01/2021 15:03:37 It's not this one by any chance is it Peter ? Probably not a a" Fly Fishing by JR Hartley" moment.But there are several Wakefield plans on the outerzone site. **LINK**
-
simple 3axis gyro(Flight controllers)
Bob Smitham replied to Basil's topic in All Things Model Flying
I use a ZOHD co pilot on a little wing 500mm span.I'm still a novice like your self it's saved me few times with it's recovery option that returns you to straight and level if you get in a panic or loose orientation .Around £35 including GPS for three flight modes and an option for return to home or geo fencing with a GPS fitted. -
Bob Smitham joined the community
-
Thanks for the settings.Been going through the Github wiki.(link for anyone going down the CNC shield with UNO route) GRBL wiki Not used Arduino since I installed a BLtouch on my printer.It doesn't take long for me to forget anything I don't do daily. A big help in setting up that avoids swapping between apps and editing config.h has been the open source LaserGRBL s/w. Can't see it being much use for cutting plans. But it does have a built in config editor allowing you to make changes and test without swapping apps and compiling .A bonus for the technically challenged and easily confused such as myself. If any one is building using UNO CNC shield This is a nice case found on thingyverse.Chosen because I had a 40mm 12v fan in my box of scrap PCBs. But there are dozens of other designs that will suit what you have lying around. Once again thanks for this.Most satisfying project Iv'e done in a while.
-
A big thank you for sharing this FlyinFlynn.The CAD files made changes to the head carriage to accommodate my unit easy.All tested and firing. Now the hard bit for me plouging through config.h files and GRBL settings for the end stop set up .Then the dialing in of settings which I imagine will be trickier than the build.