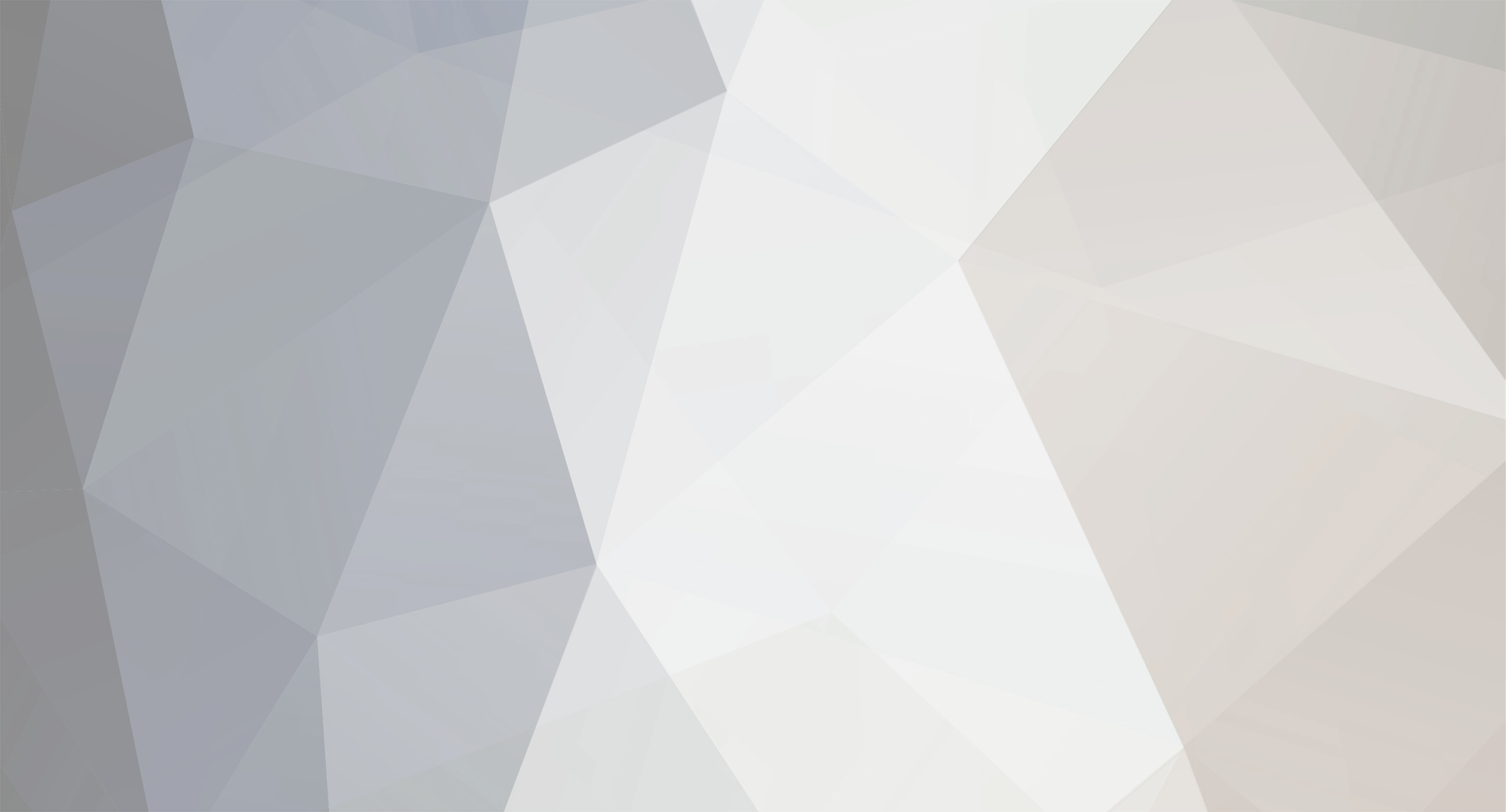
Hangarqueen
Members-
Posts
36 -
Joined
-
Last visited
-
Days Won
2
Content Type
Profiles
Forums
Blogs
Gallery
Calendar
Downloads
Everything posted by Hangarqueen
-
Fouga magister 1/4.5 moulded from scratch
Hangarqueen replied to dirk tinck's topic in Electric Ducted Fan
The designer showed them on this German forum thread about the RBC kits Fouga: https://www.rc-network.de/threads/rbc-kits-fouga-magister.11869447/page-3 I think this guy will provide you with the STL files on simple request (I know he did for other builders of the same kit) -
Fouga magister 1/4.5 moulded from scratch
Hangarqueen replied to dirk tinck's topic in Electric Ducted Fan
Well, as the Fouga has its roots as a glider, 10kg of thrust should be enough at 12kg AUW. Are you planning on implementing scale speedbrakes? I've seen some very nice examples 3D printed in other builds, even though they might not be very effective. -
Fouga magister 1/4.5 moulded from scratch
Hangarqueen replied to dirk tinck's topic in Electric Ducted Fan
I just found the info on the previous page, sorry for overlooking that.... I'll be very curious to the final weight. Phaedra -
Fouga magister 1/4.5 moulded from scratch
Hangarqueen replied to dirk tinck's topic in Electric Ducted Fan
Wow, great stuff. As (yet another) Belgian, I've been looking for a good Fouga RC model for a while now, and I'm amazed that I haven't found this thread earlier. I might have overlooked this info, but what will you power it with? Last time I saw the real thing, was in 2019, "Liberation Days" at Deurne Airport (EBAW). I'll be following this one! -
I always do a range check with the model about 1 meter above the ground, in "all" directions (I rotate the model on a stand and do the range check again) to detect any reception blind spots. Vegetation like grass (anything containing water basically) blocks out a 2.4 GHz signal in a very effective way, so make sure there isn't anything like that between transmitter and receiver.
-
I have been a very big fan of OpenTX since I bought my first Taranis around 2013 or 2014. The only thing that I disliked about it was its poor hardware quality. The long switches at the back broke off just by looking at them, and the plastic switches around the screen were just as awful as it gets. In terms of capabilities and features, OpenTX wins hands down. Not to mention the Companion program, which allowed me to bypass the very awkward way of navigating through the menus on the Taranis, and not having to use the no-feedback plastic select switches around the screen. After damaging the antenna (my stupid mistake), I got errors about the antenna on the screen, so I replaced it by a Horus X10S, which is brilliant in so many ways, except its weight and the battery life. I replaced the battery with a 2P2S Lipo, getting me 7000mAh and many days at the field before a recharge (that also takes as many days, lol). When Ethos came out on the X20, I was intrigued, but I share the feeling about a closed and proprietary system. Recently, a fellow club member sold his X20S for a price that I couldn't refuse, so I decided to try it out. First of all, I'm not a fan of touchscreen. The buttons are way too small to be practical, even with my tiny little fingers. And having to really avoid touching the screen when manipulating the radio around the field is another worry that I have. I want at least to be able to disable the touch function when I'm not programming the radio. Ethos has caught up considerably with OpenTX, but I'm still missing things like real calculated telemetry fields, using simple arithmetic. I'm used to measure current, then calculate power by multiplying it with battery voltage. Not possible on Ethos at this point. A lot of things are clearly derived from OpenTX, but implemented differently and located at other places in the menus. Take for instance the "delay up" and "delay down" on a channel. In OTX, it is in the channel setup screen, next to the "slow up" and "slow down". In Ethos, you have to use a sequencer mix (I think). All settings that you can find together in the channel setup in OTX are spread over "Mixes" and "Outputs" in Ethos. It takes some getting used to. OpenTX development seems to have come to a halt somehow, and morphed into EdgeTX. I don't know what to think of EdgeTX, but it feels to me like it is being branched all over the place to implement all sorts of features and multi-protocol stuff, which scares me as a software architect. I really like the hardware, the form factor and the weight of the X20S, even as a "pincher" (I added a tray and long sticks with integrated switches). I even prefer those aspects of it over my X10S. Except the screen, which is much brighter on the X10S. The screen on the X20S is a bit harder to read in sunlight, probably due to the touch screen layer. I have kept an open mind over Ethos, I'm starting to get used of it but still find some things awkward. Maybe it's my programmers brain that prefers OTX being more logical and organized than the "fancy layer" that Ethos is and confuses me all the time? I feel like being forced into some straightjacket of pre-programmed mixes that I don't need and don't use. Which is the very reason why I never liked radios like Spektrum; I could never figure those out. You have to find in whatever they supply as mixes and try to achieve simple stuff by endlessly combining and manipulating preprogrammed stuff. In OTX, I just select a certain channel, then add and mix whatever inputs that I want to combine. Where is the steep learning curve in that? But I keep an open mind over Ethos, and try to program my existing models in it, one by one, to learn and test. And I must admit, it's good, it works well so far. I use both radios at the field, and don't have any problems going from one to the other when changing models.
-
Love the Lysander. I used to share the landing circuit with a restored Lysander, in the nineties. It was a very impressive airplane, both on the ground and in the air (you could quickly locate it around you by the blue smoke trail it left behind ? ) I'll be following this one with interest. Does it still have the (too) long nose cowl?
-
Forum members' new models: Let's see them.
Hangarqueen replied to Paul Marsh's topic in All Things Model Flying
I've been flying the living daylights out of one of these for the last 3 years. With the slotted prop, it was extremely loud to my liking, so I started to modify it. I bought a couple of multicopter motors and props, as they are extremely efficient for this kind of thing, and mounted them directly on the tailerons. I did have to seriously reinforce those, because the forces acting upon them with this configuration is extreme. Now I have a hand-launch thrust-vectoring Su-35 with a power-to-weight ration over 1:1. I hold it vertically, give it full throttle, and it just accelerates out of my hand. It is extremely agile; it does backflips and a cobra maneuver effortlessly, and it rolls like a powerdrill. And with less noise (but still noisy, though) To protect these 3-bladed pusher props during landings, I added a couple of tail skids -
I'm sorry Paul, but I didn't quite understand what you meant. In general, and depending on the type of amplifier, you could vary the supply voltage of the amplifier and that would have an impact on the output power, but only within a limited ranged range I think. If the supply voltage drops too much, the power transistors wouldn't be able to function within their linear range. I've never looked at an amplifier this way, as it is designed with a fixed supply voltage in mind. It would be interesting to know what happens when you lower this voltage, although I'm not going to try it on mine ?
-
I have no schematic of the sound unit, but a potentiometer is a voltage divider, while a brushed controller does "chopping" of the current to a motor. So I don't think you could achieve this by using a brushed controller.
-
In my BH Spitfire, I installed a sound unit, for that extra touch. It is a wonderful Merlin sound, it really adds to the experience, but the problem is that on the ground, it is often too loud to be comfortable if you set the volume to a level that is perfect for in flight. The volume control on the MrRcSound is manual, through a small rotating knob on the side of the bottom PCB. As the sound unit is usually well buried inside the fuselage, it isn't easy to experiment with the volume. Ideally, the volume is controlled from a spare receiver channel, so it can be adjusted in flight. I thought about different solutions to achieve this, like using a digital potentiometer instead of an analog one (but I would have to add even more electronics to control it through ppm). Mounting a small servo on the knob posed two problems: - the rotation axis of the knob is inside the edge of the PCBs, and there is no room for a servo between the PCBs. Mounting it on top of the PCBs isn't an option. - a standard servo rotates over only 90 degrees; I want to be able to vary between lowest and highest volume And so I de-soldered the potentiometer from the PCB (caution, this requires some experience and patience, ans it is soldered through the PCB) and connect it through a servo cable to the unit. I could now mount it away from the sound unit. I then modified a servo by adding series resistors to the feedback potentiometer of the servo. By experimenting, I found the required resistor values to get pretty close to a 180 degree rotation range of the servo. As there was little room inside, I had to mount them outside of the servo housing. I then hot-glued everything together for testing, and it works like a charm Next step is to mount everything inside the Spitfire and take it outside for testing.
-
I built my first RC model in 1985 in a model stored owned by a very old man. I was looking for a trainer model, so he helped me choosing something appropriate. We settled for the "Ginca" from Mantua models. He recommended a Super Tigre motor for me, which I ran in patiently before attempting a maiden flight. This maiden flight ended in a stall. I repaired the model, but it never flew again since there weren't any clubs nearby that allowed IC powered models. I'm still considering to convert it to electric, just to get it in the air again, for old times sake. After training on a small motor glider, I then flew a Graupner ASW22BE vario glider in 1993, which I still fly today. Around that same time, I bought a 2m span hotliner glider for which I never found the right motor-prop combo, until recently. A fellow club member crashed his Robbe Amplitude, which is roughly the same size and weight as my nameless model. I bought the motor from him, and now it goes like a rocket.
-
Electric twin with seperate servo & RX battery.
Hangarqueen replied to Frank Day's topic in All Things Model Flying
I use dual Schottky diodes to combine two power sources. These extremely cheap components have 2 inputs and 1 output. I connect the red wire of each ESC to the inputs, and the output to the receiver. -
Today I was able to have my mother over for a visit. An important moment, her first trip outside since she had a very nasty fall on the 3th of January, when she broke her hip. Indestructible as she is, she has made a full recovery at her 88 years of age. I got the Mosquito out again for her She doesn't remember many details, but she clearly remembers some aerial combat above the woods where we used to play as a child. She saw Mosquitos and Spitfires fighting German fighters and even chasing V1 bombs. She heard the rattling of their machine guns, being scared to death. She remembers running to their shelters as they heard the droning of the bomber squadrons approaching. She still remembers vividly the terrifying sound of the V1 bomb, and hearing the engine stop, followed by a loud explosion nearby. What a horrible time that must have been. My father, who passed away more then 20 years ago, used to tell his story about low level aerial combat between a Spitfire and a 109 above his head, when he threw himself to the ground in a field. He grew up really close to the airport, hence they were close to a popular target. War is never beautiful.
-
Well, to be honest, I feel that the BH Mossie flies better and more stable then the Freewing one. I never had the Parkzone, but a fellow club member had a similar incident with one. One engine quit and he drove it into the ground like a fence post. The Freewing Mosquito had extremely long motor/propeller shafts and 3-bladed props, which meant that in case of a belly landing, chances were that you had a bent motor shaft. SO I avoided doing belly landings as much as possible, but due to all the trouble I had with the retracts binding, I had to do a few of them. When I looked for a new Mosquito model, I had a look at the Seagull version too, but then I read all the horror stories about them. Too many crashes to my liking, it can't be a coincidence anymore. It's a shame, because it's a beautiful model. I wish I had the patience and the skills to build a BT Mosquito. But I'm preparing my BH Sptifire again, can't wait to have that one in the air again. Wonderful flying model, great presence in the air, a real shame and very surprising that it isn't that easy to get by in Europe. I love Erik "Winkle" Brown's stories too, I have his autobiography, and it is just stunning to read about his experiences. He was a pilot pur sang.
-
My experience, again with the foamie version, is that with full flaps and engines at idle, it drops like a brick. I had to land it once like that, due to an incident. I took off normally, when suddenly the model veered aggressively to the right. As there was an active runway on my right where I flew then, I had to act really quickly. I couldn't counter the strong pull to the right with either aileron nor rudder. I cut the power, and immediately regained control. I called emergency and landed at idle, but it was a rough landing, very hard to do any flare at all. What happened was that I had an older 4S battery of which the voltage sagged too much at full load. I had two ESCs, one of them called it quits with that low voltage and went into Low Voltage Cutoff.
-
Thanks Chris, I will be practicing that full flaps approach in the next landings. I guess I was apprehensive about this because it didn't go well with the foamie version, which had a very strong tendency to nose over after landing. And that tendency was stronger with full flaps, probably because the full flaps blocked out the airstream over the full up elevator that was required to keep the tail down. This Mossie doesn't have that tendency at all, so I should be fine with full flaps.
-
The matt finish is something that I really need to apply too, looking much better!
-
And then the day of the maiden came. I had been waiting for weeks in a row for some good weather during my free time. Last week there was this one day when the wind was very calm, but they forecasted rain. While I checked the forecast, I saw that I had a window of about one hour left before the rain started, so I quickly loaded the Mossie in the car and drove off. Assembly goes really quick, last preflight checks, hat camera on, and ready for departure I have video of the first two flights, but I seem to hold my head up too high for a good framing. So I took a couple of still images from the video material and cropped the "good parts". As already mentioned, it tracked heavily to the right, which surprised me a bit. The climb was more than powerful enough to look non-scale I only did some turns around the field, just to get it trimmed out correctly. I left the gear down because I didn't trust it yet. It took a couple of attempts before my approach was right. I tried out "half flaps" at altitude, and noticed no real ballooning, so I used this setting for the first landings. As this flaps setting didn't cause much drag, the approach had to be long and shallow, which isn't easy with a camouflage model on a green backdrop. I will add landing lights to facilitate this. In short final, as I eased the controls for the landing, the model veered to the right again, causing the right wing to drop a little. I let this surprise me, and the Mossie landed on the right wheel first, causing the gear pin to bend, as mentioned above. I made the reinforcements and had a second flight. As you can see in the picture, I landed again at the right side of the runway. But the landing was much better, with a little bounce. It is visible in the picture that the landing gear isn't in its normal position anymore, as it came loose. But I felt happy with these flights. It flies really stable, solid, powerful climb, scale speed in the air. But I noticed that I couldn't really fly hands-off for long, and the tracking to the right bothered me. Post-flight, I had a look at the telemetry log, and noticed a constant offset in the rudder channel. I then remembered that I programmed a sub-trim (which I normally don't use, I prefer to center flight control surfaces in a mechanical way), because it was impossible to center it mechanically (due to my integrated rudder servo and custom control). I then looked at the rudder again, and notice that even though the top of the rudder aligned with the vertical stab, the bottom of the rudder was clearly off-center. Even better (?), it was deflected to the right (!). That explains a lot of the difficulty that I experienced with the tracking, and even the deviation in short final (also to the right). While looking at the rudder, I noticed another problem: the tail wheel hinge had broken off: This mean disassembly of the whole tail cone assembly, and installing a solid metal hinge that I found in the local hardware store This will hold a lot better. I took advantage of rearranging the tail wheel position while extended, because it sagged a bit too much when the weight was on it. Both positions are now closer to scale too: I had to correct for a warped right aileron too, which was pointing up at the outboard side (which would also contribute to a pull to the right). And before the second flight, I made another improvement in cable routing. I found the motor wires uncomfortably close to the elevator servo, so I installed some hooks to keep them away from the servo Disregard the large XT90 connector near the servo, that is from the disconnected flight battery. All in all, I'm happy with where this model is now, and can't wait for another good flying day. Way too much wind this weekend, so the wait is on again. Meanwhile, I can prepare this other beauty for the next season
-
Motors and spinner were a different story. As we can only fly electric on our field, the choice is simple enough. I'm a fan of the eCalc application, with which you can find a good estimation of the performance of a given motor and prop combination. As it is a Mosquito, I really wanted a 3-blade propeller. I ended up with an NTM 3548 900 kV motor and a Master Airscrew 11x7 "-bladed prop. According to eCalc, this should be some sort of overkill for this model In reality, it was a lot less. Telemetry from the second flight showed a total power of 1200W, instead of the calculated 1600. Airspeed seemed to correspond closer. But first the installation. The original firewall is designed such that it can easily be moved forward or aft, depending on which motor one is using. When I first trial fitted my combo, it was clear that the whole assembly had to be moved as much forward as possible for the spinner back plate to end up in front of the cowl. I did have to glue in some reinforcement then, to allow for the pull of the motor on the engine mount and support. I also ordered a set of spinners from Sarik in the UK, which were a perfect fit and very scale shape, but I couldn't center them properly. That was due to my lack of skills, not to the product. I decided to give some spare spinners from my foamie Freewing Mosquito a try, and to my joy I found that they were a perfect match in size. I only had to "dremel away" some material at the back of the back plate to get the prop adapter to fit. That was within my skills limitations ? They look fabulous! Again, I couldn't resist having a look at the assembled model, and I was very pleased with the looks Then came the time to prepare it for a maiden flight I chose to insert a soft balsa support at the bottom of the nacelles, to protect them from breaking in case of a belly landing. Also fitted mounts to connect the back of the nacelles to the front part The flight battery is inserted from the front, I added a vlecro strip to keep it securely in place The canopy was originally intended to be kept in place by a couple of plastic bolts at the back. That appeared to be extremely fiddly, so I replaced those with some strong magnets. They are so strong that I had to add a small handle on top of the canopy, to pull it loose from the fuselage. But it works really well. I then started assembling everything again, when disaster struck. While softly (I have the physical strength of a chicken...) tightening the propeller nut, the threaded shaft just broke in 2 pieces I opened an RMA with HK, and to my surprise they accepted this and sent me, after a very long delay due to the Chinese New Year, a replacement prop adapter These adapters seem to be made of a very soft Aluminum, hollowed out to accept a bolt to hold a spinner. As my spinner is attached differently, I decided to insert an M3 bolt for reinforcement of the prop shaft I had to grind off the contours of the bolt head, to allow the prop nut to pass And now she was really ready for a maiden flight
-
Thanks Chris for your input and views on this. I totally agree on your viewpoint on this. We actually have to choose the weak point in the construction, as "something's gotta give" ? Our flying field holds a couple of challenges, due to serious airspace limitations on one side of the runway, making nice, long stable approaches almost impossible at times. I'm hoping that this last modification will just prevent the pin from bending or coming undone from the retract. My guess is that if I were to have a really heavy landing, that the retract would be torn out of the nacelle, or the struts bent or something of the sort. As for the play on the flaps, most of it comes from the fact that the connecting wooden dowel doesn't fit snugly into the openings of the nacelle where it goes through. I misjudged this when I glued everything together; I should have secured this in a better way. I don't know what you mean by "rod tangs"?
-
Assembling the model at the field should go as easy and predictable as possible. Each wing contains 2 servos (aileron and flaps), an ESC and a retract. I decided to combine these 4 channels into an 8pin MPX connector for each side. Normally I would solder a male connector to one wing and a female on to the other, to prevent mistakes in connecting them at the field. But in this case, I mounted the male connectors to a thin plywood plate that would be then fixed inside the fuselage. The spaghetti of wires that will be hidden: After the fixing of the plywood support plate into the fuselage, things look a lot neater: Impossible to make mistakes at the field now. While soldering, I had to take into account that I would have 3 power supplies available: one from each BEC of each ESC, and an extra separate receiver battery with a 10A sBEC. As I was going to use an RB20 from Frsky, it supports dual power supply, I usually use one power supply input for the receiver battery/BEC, and one for the ESC BEC. As I have 2 ESCs, I combine their 5V output through a dual Schottky diode: This has proven to be a very reliable solution, for a relatively low cost and a high peace of mind. I then tested each power supply separately, to make sure that I do have the redundancy that I think I have. When assembling the model again for an all-up test, I got a nasty surprise: Clearly, something was wrong. Either it was a warped fuselage, or a somehow bent wing tube. The wing tube was bent allright, but luckily I could find an easy replacement, even with a larger wall thickness from the local hardware store. When put next to each other, the bend angle of the original is clearly visible: But oddly enough, that didn't solve the misalignment of wings and horizontal stabilizer. In the end, I solved this by shimming the latter at one side by 1 mm, and that literally set things straight.
-
Forgot to mention a couple of things. This is how the hinge of the tail wheel assembly broke, near the hinge axis I am currently replacing this with a metal hinge that I bought today in the local hardware store. And while the tail section was open, I took a picture of the reinforcement that I did for the "lip" at the front of the top part, by adding a plywood rectangle on top of the lip, and enlarging the opening in the fuselage part, to accept this plywood part. As the tail section will get its share of forces, I can't take any risk here.
-
Next up were the flaps. Originally, a servo would be mounted on the bottom of the wing (intrados), connected to the inner flap. The inner flap would be connected to thbe outer flap via a thick steel bent wire. There is nothing wrong with that, except for the visual aspect. Which is even negligible. But I wanted to change it anyway. Too much time. As there is plenty of room in the nacelles, I wanted to move the flap servo inside the nacelle, and control both flaps from there. Only problem was: where to mount the control horn on? I first did a small experiment, by using a wooden dowel to connect both flaps, ad then somehow mount a control horn on the wooden dowel The control horn appeared to need a very awkward angle on the dowel to get a straight connection to the servo. I then decided to make a slit into the dowel, in which I could then insert a plywood plate, which would then in turn be glued inside the flap leading edge. This will ensure a solid connection between the dowel and the flap itself, considering the serious aerodynamic forces to be expected. And then the servo could be connected. And then finall, everything could be positioned and glued into place. To be honest, this solution leaves more play on the flaps than I anticipated. If I were to do this again, I would provide more of a guide for the wooden dowel.
-
Adding the tail wheel steering complicated matters for the rudder control. No way that I could cram in another steering arm. The only solution left was to install the rudder servo into the vertical stabilizer. First I took a scrap piece of brass, cut it to size, drilled holes in it, then soldered a collar to it This collar then accepts the steel wire that is attached to the rudder. I then bent a steel wire and cut it to size, giving me a snug fitting rudder control system: To the left is the rudder servo, sitting inside the vertical stab. To the right, my control horn attached to the rudder hinge line. The part of this build that took me the most time probably, was how to install the tail section with the horizontal stab, and how to make this removable. The forward part has some sort of lip that inserts to the fuselage (left on the picture above) . This lip really needs to be reinforced, it really doesn't feel very strong. This is the easy part. After a lot of consideration, I opted for the following solution: insert a 3mm plywood wedge with a blind nut, which accepts a 4mm nylon bolt that goes straight through the tail section and the horizontal stab: The top of the (sunken) nylon bolt can be perfectly covered later The rest of this construction is perfectly accessible from the bottom Tail section done. For now.