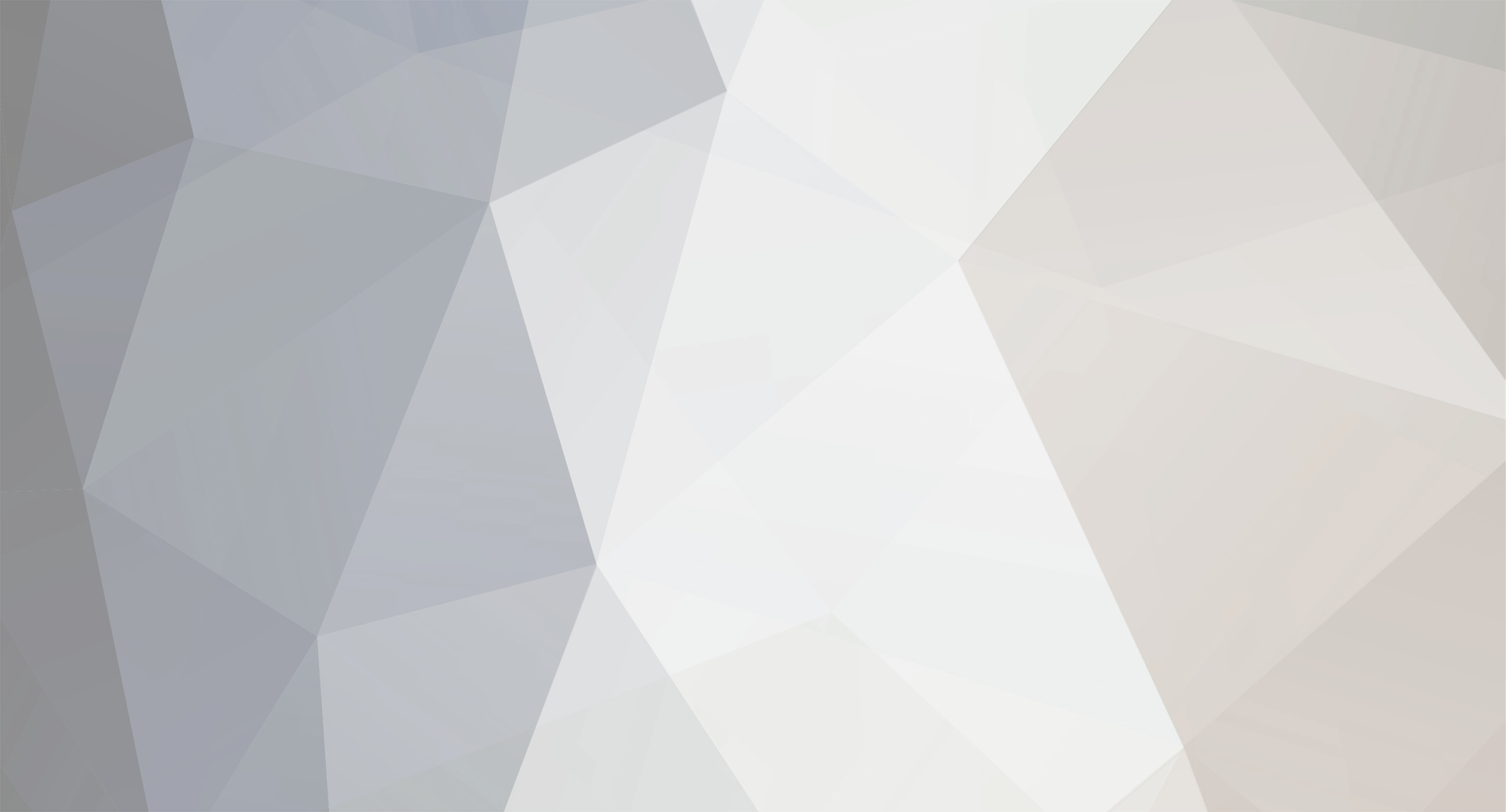
Terry Whiting
Members-
Posts
386 -
Joined
-
Last visited
Never
Content Type
Profiles
Forums
Blogs
Gallery
Calendar
Downloads
Everything posted by Terry Whiting
-
Building the Nijhuis Lysander
Terry Whiting replied to rookie jim's topic in Tony Nijhuis plan builders
Jim, I sympathise as I have received many such bites. Before I became a manager on Royal Mail I had 25 years as a postman and have the scars to prove it. I think that hand will be out of service for more than one week. Terry -
Building the Nijhuis Lysander
Terry Whiting replied to rookie jim's topic in Tony Nijhuis plan builders
Hi Guys, Just incase anyone tries to message me or puts a question to me in this blog, I wll be out of the running until Tuesday 16th as I'm changing my broadband server.. Cheers TW -
Prop, Sorry, can not remember, but you would be safe at 25% of the chord being a parallel chord wing. To answer your question, 3 5/8" ==== 93mm. What is the chord measurement of the wing? TW
-
Building the Nijhuis Lysander
Terry Whiting replied to rookie jim's topic in Tony Nijhuis plan builders
Geoff, I can not see any problem with that set up. Mario's method on page 6 shows the fuselage upright which is similar to my own method. I just made two equal size block which when place under each tailplane tip lifting the fuselage belly clear of my building board. With my fuz square (upright) to my building board, I knew then the tailplane was square to the fuz, just left the normal tip geometry. So mix that epoxy -
Carbon u/c for Lysander
Terry Whiting replied to Allan Bennett's topic in Tony Nijhuis plan builders
Congrats Allan, I'm afraid even if I was ready for a maiden, this weather is a NO NO for me. My days of playing the Brass Monkey are past . After reading you ran out of up trim I wondered if it was an incidence problem, I must admit I had not checked the plan incidence. In doing so I found it was 2.5 degree + on the wing, and zero on the tailplane. Can see no problem there, so as you suggested.could be a balance problem. I think I will do some ballance point checks using the mean chord. -
Building the Nijhuis Lysander
Terry Whiting replied to rookie jim's topic in Tony Nijhuis plan builders
Hugh, I do not know the grade of mine, but you wouldn't bend it by pressure alone, even when annealed it required a good vice and hammer, but I'm sure yours would have less stress marks if annealed. I would file off that sharp aluminium angle too. No you must not quench, just let it cool naturally. MT, wow, 56mph thats a scale speed just over 500 mph. Terry Edited By Terry Whiting on 07/03/2010 17:42:08 -
Building the Nijhuis Lysander
Terry Whiting replied to rookie jim's topic in Tony Nijhuis plan builders
Hugh, The UC looks pretty good to me, but I doubt if mine would have looked like that if I hadn't annealed. TW -
Building the Nijhuis Lysander
Terry Whiting replied to rookie jim's topic in Tony Nijhuis plan builders
Hugh, Have you tried annealing, I had to anneal the aluminium that was kindly given me by John Laverick, and it worked just fine. TW -
Kevo, Go to "Beginners" topic and scroll down to 'C o G by Hogster' (28/2/2010) This thread may help you.
-
Building the Nijhuis Lysander
Terry Whiting replied to rookie jim's topic in Tony Nijhuis plan builders
HI Keith, Welcome aboard. Your aluminium enquiry....... Look up page 18 of this blog and you will find a thread by placed Hugh Philips on the 18/2 on where you can obtain your aluminium. What stage are you with your Lysander? TW -
Are we an ageing hobby?
Terry Whiting replied to Biggles' Elder Brother - Moderator's topic in All Things Model Flying
1; Just coming up 78, sold off all my IC, went electric 2 &Electric;Sport&; Semi Scale EDF Water planes 3.& Rubber, 66 years ago, but can't recall it's name Edited By David Ashby - RCME Administrator on 10/03/2010 15:05:56 -
Building the Nijhuis Lysander
Terry Whiting replied to rookie jim's topic in Tony Nijhuis plan builders
Hi Jim Yes that is the reason in having to sand the rib's spar cut outs. I can remember it stating in the build instructions to pin the main spar directly to the board. To do this the ribs will never sit properly on the spar. To make life a little easier use 6mm sq Balsa strip as your main spars, as Obechi is unnecessary for four relatively small wing panels. If you have some oddments of the 5mm sq stringers, use pieces as packers under the mainspar, your ribs will then fit perfectly on the spar, and their TE (aileron hinge spar) will sit nicely on your board. If you check on the Lysander build of Tony Nijhuis, you will see he used packers. -
Simon, Wonderful. Have you tried any down thrust? I do not think the fullsize had down thrust, but then the prop was only doing 1200rpm. Might be worth a try before altering the tailplane. TW
-
Carbon u/c for Lysander
Terry Whiting replied to Allan Bennett's topic in Tony Nijhuis plan builders
Allan, Remember, ........patience is a virtue. I do not think we will be seeing much maiden flight weather for a while, this damnable wind and rain is relentless. A shame it required 4oz of ballast, but I think most will come out at about 6lb + mark. My dural undercarriage is 3.5oz heavier than your home made carbon fibre job, which I must add you made a really good job of. I'm using Tex which has a slight weight penalty of about 5g per squ ft. but it all adds up TW Edited By Terry Whiting on 28/02/2010 09:56:27 -
Building the Nijhuis Lysander
Terry Whiting replied to rookie jim's topic in Tony Nijhuis plan builders
Jim, The pleasure was all mine. I didn't enlarge the hole for the axle as I didnt know what if you were purchasing ready made threaded axles, or was going to use a harden bolt, but whatever you use it will require redrilling to size. As for sheeting round the fin and 'stab', use a piece of cardboard such as a serial box and cut a template. Yes remove the covering where glue is to be applied, and check ( PAGE 6) for Mario's sketch on fuselage jigging for stabilizer alignment. Before gluing the 'stab', stick a pin in each tip. If you use a long straight edge place it lengthways on the hinge spar then your pins will exact in each tip. Now measure dead centre of F5 and insert a 3rd pin, now adjust the 'stab' so the the measurement from each tip pin to the pin of F5 is dead equal. You are now ready for gluing. Leave the tip pins in place as they will be required for fin alignment. When the 'stab' is set slip the fin into position, and stick a pin into it's tip. Take a length of white cotton and tie a loop at one end, pass the loop over a 'stab' tip pin, pass the cotton over the fin close to the pin and down to the other 'stab' pin. Just hold it against the pin making sure there's no slack. Mark the cotton with a pen exactly level with that pin. No measure the overall lenth from loop to ink mark, half that measurement exactly and mark the cotton in the centre. Replace the loop to the tip pin, over the fin,and hold or wind the cotton around the other pin. Adjust your fin the the half measured mark and your fin is dead upright and ready for gluing. -
Hi Simon, How is the world in your area ? , certainly not test flight weather in Hertfordshire. I think this winter will make flyers think more of the advantages of indoor flying. It is certainly making me think. TW
-
Building the Nijhuis Lysander
Terry Whiting replied to rookie jim's topic in Tony Nijhuis plan builders
Hugh, In not purchasing the wood pack I can not answer, but I would think Peter's answer is right, as I believe the two sides were handed to give the side thrust. My fuselage box was constructed with 2mm hard balsa sheet, the notches in the formers from F1-F6 were made 1.5mm wider to allow for 1.5mm birch ply doublers. The scarf jointed idea did not appeal to me. I built the fuselage square without side thrust as it so is simple adjusting side thrust with electric motors. -
John, I think you were being pedantic. This is a thread for beginners. I thought Timbo's chart was and is a damn good guide for any newbe to this hobby. I'm sure when you entered this hobby you were not concerned about the forces of torque when using your bog standard servos which at the time I'm sure were the only servos available.
-
Building the Nijhuis Lysander
Terry Whiting replied to rookie jim's topic in Tony Nijhuis plan builders
Well guys Monday of this week was great to get back into my model workshop/den, being confined to barracks (the house) for nearlly 4 weeks seemed an eternity. The rear end of the fuselage is now completed, including the fitting of both fin, stabilizer, and covering in that area. Have fitted two servos (rudder & elevator) via the canopy, they live just forward of F7, both are connected by closed loop (pull-pull). A removable false floor is their cover. The fullsize Lyzander has a fuel tank between the wing carrying structure which in our model is F4 & F5. I replicated this with 1mm sheet. It does help to fill a greenhouse of a cockpit. I have desided for the instrument panel to use photographic instruments, just too many bezels to turn on the lathe...... Next I will turn my attention to the undercarriage. TW -
Building the Nijhuis Lysander
Terry Whiting replied to rookie jim's topic in Tony Nijhuis plan builders
Doug, TN has his own methods of building, I have my own method so I never build by instructions. The tailplane ribs do not have a 'top' as they are symmetrical. The finished tailplane should have an equal taper to it's top and bottom. If it is built inverted and flat the tailplane will have built in dihedral to the under side. If you are interested this was my method. 1. All the T ribs had a1.5mm strip removed from dead centre of each rib. 2. From 1.5mm sheet I produced an overall plane size tailplane including tip blocks. , Carefully marked all rib postions exactly to both sides. 3. The 1.5 sheet tailplane is pinned to my building board, pin but do not glue a length of 6mm X 6mm as a straight edge for what will eventually be the hinge spar. 4. Now glue the half ribs in the respective positions, but not to the 6mm square. Cut 2 piece of 3mm sheet for false leading edges to the taper of T1-T5, 5, Remove 6mm square, and cut 4 pieces of 6mm sheet to the taper of T5-T1- T5 ( double tapered lengths) for hinge spar, and glue in position, remember to add hinge blocks. The other pair are for the elevator. 6, When dry sheet over in two panels. it can be done in one if moisten the sheet in the aera of T1, but I prefer 2 panels. I did not include any main spars as being a small tailplane and completely sheeted making it is unnecesary, but fit them if you wish. 7. This was left to dry overnight, when removed from the board you will find it absolutely rigid, so rigid there is no neen to pin down to replicate side one. 8 Sand false edge level, and add leading edge. As I wished to save a gram or two once I had maked all the rib positions on the 1.5mm core I also marked the hinge spar and FLE, then using a piece of 5mm squ I marked inboard of the ribs, hinge spar and FLE . This was all cut out before the 2nd side was l sheeted. My fin was also made as above. My elevator was also be built on a 1.5mm one piece core which also included the tip blocks. Pin down the core, glue double tapered length of hinge spar, and add riblets, leave to dry over night, remove from the board and add the other sides riblets. I only cut out the elevator centre section after the torque rod was fitted, this give a perfictly inline elevator. Including your tips in the cores gives a better for block gluing for tailplane,and elevator tips. It might sound a long winded process, but I can assure you it's not. Edited By Terry Whiting on 24/02/2010 10:45:33 -
Kieth, 3 blade props only look nice stationary, and the only time I used them was for static shows. For flying that extra blade is drag which in your case reads in higher amps . E-Max CF 2812 has a continious current rating of 10 amp and really was developed for fast rpm 5" props.
-
Keith, I think you are running too close to the edge here in using 12A ESC, as you are drawing almost 11A per ESC, and surely that battery pack can not be fully charged
-
Nijhuis Hurricane in foam
Terry Whiting replied to Toni Reynaud's topic in Tony Nijhuis plan builders
Hi Toni, How did you get on with your paint job. After the disaster of your first canopy I must say the second is first class What was the weight penalty in using brown paper? TW -
Building the Nijhuis Lysander
Terry Whiting replied to rookie jim's topic in Tony Nijhuis plan builders
Mario, No my friend I'm no perfectionist, I have just acquired different methods over the years. A model plan is like a sheet of music, we can all select diferent instuments, but at the end the day we all play the same tune. Edited By Terry Whiting on 21/02/2010 11:25:04 -
Simon. Although to scale these control surfaces are extremely powerful for the model's weight. When I converted the Widgeon from free flight to RC I was experiencing the very same problems with elevator and rudder. I was in fact letting RC cloud my mind. It had been flying beautifully as a free flight so WHY?? It then dawned on me the only trim I had on the fin was 1"x 1/4" piece of soft thin aluminium, and the stabilizer was trimmed with pieces of thin card. In my conversion my rudder was 50% of the fin area, and the elevator was 25% of the tail plane area. Today my FULL throws are about 3/32" either way, and I couldn't guess how little control movement are required in flight. Edited By Terry Whiting on 21/02/2010 10:49:06