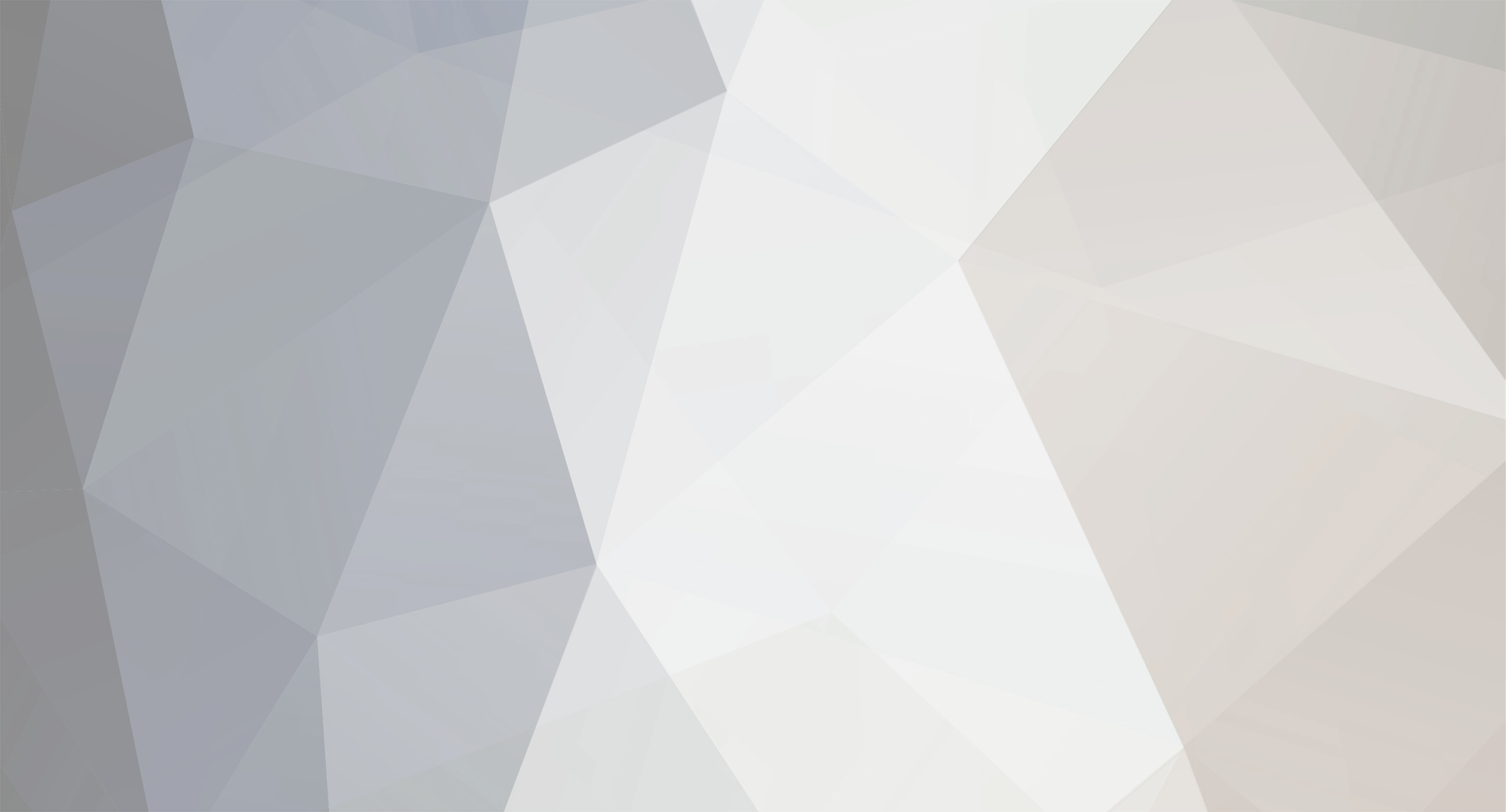
Peter Beeney
Members-
Posts
1,696 -
Joined
-
Last visited
Content Type
Profiles
Forums
Blogs
Gallery
Calendar
Downloads
Everything posted by Peter Beeney
-
BMFA subs increase.
Peter Beeney replied to john stones 1 - Moderator's topic in Flying Sites and Clubs
I’d have thought that the expression ‘due mainly to significant increase in claims’ was fairly unambiguous. I’m reading this to mean that there has been an increase in the number of claims made; and the wording immediately before this is certainly implying that these claims have been payed out as well. So perhaps the question should be ‘Why is this increase happening?’ Or maybe a touch more succinctly ‘To what extent are these accidents actually assessed and evaluated? Hopefully Manny might go some way to answering this (for me) in the forthcoming Chacksfield Chat. If an Insurance Assessor came to our site on a General Inspection and we explained the situation I’m pretty sure we would fall within his field of acceptability. The parked cars increase the pits area in total by about 30%, at a guess. But everything is now consolidated in one small area; and compared to the size of the surrounding countryside that we fly over this is a very small percentage indeed. Also in common with all other clubs there is a strict no go zone between the runway and the pits. With the best will in the world the odd transgression can happen, this would be subjected to some banter, such as ‘Red card called’. But it’s always accepted as accidental, there but for the grace of God etc… If it was considered to be deliberate the club as a whole unit would decide on any further actions. If any previous record was also taken into consideration this would get a clean bill of health too. Sure there is some occasional indifferent flying and maintenance but any crashes always happen in the flying area and are no danger to anyone; this may well be a sort of universal situation perhaps; I’m sure we act more or less as others do. I only know of one insurance claim, sometime in the early eighties. A building leapt into the air and smote a model between the wing bolts, dislodging 3 tiles in the process. The modeller paid £80 for them to be replaced and the BMFA reimbursed this by return. I don’t know of anyone that’s had any car damage inflicted by a model. So how often is any sort of insurance claim happening; is it frequently or rarely? Again perhaps we may get an insight to this soon. PB -
BMFA subs increase.
Peter Beeney replied to john stones 1 - Moderator's topic in Flying Sites and Clubs
I’m a little concerned here that the safety element in all of this seems to be missing at the moment. The nonchalant statement: ‘there is a good chance this year we won't get the refund, due mainly to significant increase in claims for members crashing into other members vehicles or expensive aircraft in the pits area.’ looks like just a pretty bald reason for increasing the subscription in this context but if I take it at face value, which I have to at the moment, then it reads as if model are almost routinely crashing into cars (wherever they are parked) and pits areas. This is rather a common political get-out manoeuvre nowadays; “ We’re short of money.. again ..so we’ll now have to charge you even more..” Hopefully there may be an explanation re. safety forthcoming in the near future. I feel that if I were in any way skeptical about it at all I would be a bit suspicious and would be inclined to prompt some sort of an investigation. I’m not particularly concerned about a £4 increase either, although going too far too fast might just trigger a spiral of diminishing returns. On the other hand, another political trick might be to set the demand high and then on the day reduce it somewhat to create a feeling of relief. We shall see… I wonder with regard to the falling numbers if in part the BMFA might have identified a steady decline in the number of younger members joining over time. This is apparently happening in just about every other other older and established pastimes / hobbies. Newer activities are taking over; and perhaps with some hindsight it will be seen in the future as being on an exponential curve. If so, then this might be difficult to divert or reverse. I was once told that the average age of BMFA members was 57… …and rising. If the average looks of our mob are anything to go by I’d say that might be a trifle optimistic… However, despite our general well weathered demeanour we don’t have any problems with multi-rotors or helicopters or indeed anything else. Just get out there and fly it! We even have a little car track, this is for use when it’s a bit wet or windy, but it gets a bashing anyway. Worth more than five good laughs a minute. If the pits area, 30 metres away from the operational runway and in the strictly strictly dead air, is considered to be safe enough for pilots to congregate why exactly is it not considered safe enough for cars? Which are only inert objects after all: and if that nonchalant statement above really is a straight line then it doesn’t really seem to matter now where you park and pit. The casual sign-off -‘ Take care ’ - really does now seem to have a certain ring about it at the moment… Take care PB -
BMFA subs increase.
Peter Beeney replied to john stones 1 - Moderator's topic in Flying Sites and Clubs
The gentleman that told me about the car damage did have access to the facts and figures and although he never disclosed any information, or even make any serious comments really, he did infer that he thought that the claim figures were artificially high; and this was around 1980. I’ve no idea how the system works now but back then for small claims at least the insurance just paid out on demand. Regarding the car parking, our procedure is slightly different. We line the vehicles end on adjacent to the back of the pits area, backed up or forward facing, whichever suits. This started when I was flying at a site in the same circuit with full size gliders. The instructors there were overall in charge of proceedings and they liked to see us all lumped together in one place rather than wandering about all over. So we justify this for the same reason, there are no bodies ever traipsing between the pits and a remote car park. No one has ever had any issues with this, indeed I’m sure that all are happy to be able to unload and reload with an absolute minimum effort; and happy pilots always help to maintain a permanently relaxed atmosphere. Another problem I have is wondering that if a remote car park is considered to be a safer area than the pits then why are the pits not in this area? Surely personal safety should be the first consideration? Staying with safety matters a very important point (for me) is the fact our car park now doubles as a something of a safe area. If a model goes out of control and a warning is shouted then all persons can take refuge by ducking down between the cars. I’d much rather the model doesn’t hit anything but if it has to be then a car is much preferable to a human being. By a few hundred percent just for a start. Even the insurance company would consider it to be first choice, I’m sure. It’s not infallible of course, the model could still hit you but it does lessen the chances. I have thought occasionally we should practise this because then folks might have a sub conscious reflex if they’ve done it before; and with the latest revelations from the BMFA in J Stones 1’s OP tomorrow might not be a moment too soon…… Incidentally I’ve never seen a model hit and damage a car. PB -
BMFA subs increase.
Peter Beeney replied to john stones 1 - Moderator's topic in Flying Sites and Clubs
Nigel R @ 11/09/2018 12:44:54 Exactly so, Nigel, I was thinking along those lines too. I wonder why a BMFA representative (Safety Officer?) hasn’t at least commented on this; …or perhaps he has, but it’s a little bit unprintable… Kicking the figures around a little bit, if I assume £350,000 paid out annually and each average claim is for £1,000, then that’s the thick end of a claim a day by my reckoning. Purely as a point of interest the average cost of a vehicle insurance claim is quoted as being £2,936. At first glance this seemed to be quite low… A friend who was a BMFA Officer told me in casual conversation many years ago that the biggest single item claimed for was car damage. By far. So probably that’s aways been so. But that so many models appear to be crashing into into the pits area was certainly the most significant statement in that communication for me. It slightly reads as though it’s almost a common occurrence. PB -
Looking at the wire size discussion from yet another slightly different angle, all the motor input traces I’ve seen show a rectangular wave form with sloping leading and trailing edges. So maybe the input is not particularly sinusoidal, indeed I believe a sine wave is actually quite difficult to create with other than a rotating machine. One way of describing a sine wave is to call it a square wave with all the harmonics removed; so maybe removing all these very harmonics is the problem… Fortunately most devices seem not to be that fussed about their input anyway, they just carry performing as normal. I’v e always thought that the “is it AC or is it DC” question is a bit of a grey area. DC into the ESC, but this is an inverter, it converts DC to to 3 phase AC; so AC out to the motor. There are 6 switches inside, arranged in what is known as half H configuration, each wire connected to the output of 2 switches. The other ends of the coils are all connected together within the motor to form the star point. The switches are timed to switch in pairs to create the reverse direction of the current once every revolution of the motor. It has to do this or the motor won’t run. Or even start to run. I wouldn’t be convinced that the PWM’s frequency is varied, rather that stays fixed, say at 20KHz, and each cycle (Hertz) has an on on-off period. If the on-off is equal in length over one cycle then the average voltage over the cycle would be half. A 10 volt input would therefore be reduced to 5 (average). Varying the input voltage to a motor is perhaps the easiest way of varying the speed. In practical terms if you measured the input to the ESC with a DC clip on meter on one leg you might get a reading of say 20 amps DC. If you wanted to check the current in the motor wires you would need an AC meter. Measuring one wire you would see the same 20 amps. Clip over 2 wires and it’s essentially the same but if you include all 3 wires you would read zero; this is because the instantaneous current in all 3 wires at any one instant adds up to zero. Actually you might occasionally see something like 0.5 - 1 amp, this is most likely because the winding resistances are not precisely the same. Looking at the winding wire size I think to get a handle on this we need to consider again the back emf. This has been quoted a few times before, as I recall. When the motor runs it generates a back emf which opposes the input voltage in equal terms; for the sake of this discussion anyway. Considering a motor with a kV of 1,000, a resistance of 0.03 ohm, 30 milliohms and an input voltage of 10 volts. When the motor is running unloaded the back emf will virtually equal the input voltage. (For this argument). Now we fit a prop such we have 20 amps of current flow. For this current to flow through a resistance of 0.03 ohm we need a forward voltage of 0.6 volts. This in turn means that our prop has reduced the revs by 600, - each rev = 1millivolt. A bigger prop results in a 1,000 rev drop, emf = 9V, so now there is one volt applied to the resistance, current flow is now 33.33 amps.That is 33.33 watts dissipated as heat. if an even bigger load reduces the revs by 2,000 then the volts have doubled to 2 resulting in a 66.66 amps current flow. But the watts dissipated have increased significantly, to 133.33, that’s a x4 heat increase for a x2 voltage increase. A little pointer as to why the motor can sometimes start to warm up quite quickly. Taking this to it’s end point, the motor at a standstill but the full 10 volts applied results in 3.3 kilowatts dissipated as heat; plus copious smoke and maybe a few flames as well. So in general only a relative small voltage is actually only ever applied to the motor windings. Because the ESC to motor wire lengths are usually very short I guess they don’t really have to be that big. The back emf also has another very important function too, it times the switching sequence for the ESC. I suspect this voltage will be sinusoidal because it’s created by the rotary motion of the motor. Hope this makes some sense to someone… PB
-
I’d not seen that Splice before, Nigel, it’s very tasty, but as it happened my technique was \ is rather more simple and straight forward. My ‘test piece’ was done exactly as per a normal joint so for that I took a piece of 35 MHz rx aerial sized wire, cut it, trimmed about three sixteenths of an inch of insulation off each cut end, tinned the bare ends, laid them together overlapping for the length of the trim and just touched them with the hot iron. I very much suspect that many folks also do it exactly this way too… To give it a serious workout I clamped it in the bench vice with the join hanging down underneath. Then I hung my power drill box on the end and gradually placed weights on top of that until something broke. I suppose I did this trick in all about 10 times to get a fail average, (I only think in belt and braces terms), and in each case the wire broke just where the solder stopped and the bright copper wire was just under the end of the insulation. The break was always close to the solder joint but it never was the actual soldered joint. After that I decided that I’d just keep soldering on regardless… No idea of the total weight involved unfortunately, surely a few lbs though, I was just interested to see the joint part; and indeed, in all honesty I thought that was exactly what was going to happen! Maybe the ‘expert’ was a serious practitioner of dry soldered joints in his day… Another type of join might be to form a U in each wire end and then hook squeeze and solder them together. Break that if you can… Battery connections done in just the same way. Staggered cut by about half an inch, followed by the same little overlap solder jobby and finally a piece of silicone fuel tube slid over the whole caboodle. Only takes about half a day, or perhaps even a lot less than half an hour, to do. I thought it might make a convenient point to cut an old pack out or test the pack voltage for whatever reason but in the event I hardly ever needed to do either. I’ve also soldered a couple of big motors to their ESCs in the past. Same way as I did the flight pack cells. A big flat sided chunk of copper iron heated hotly with a blow torch, then the two well tinned ends held against each side, the iron then slid out and the ends instantly butted against each other. That was about as elegant as I could get and I never had any problems. At least, not with that arrangement anyway. Unlikely to do it again though, connectors are much easier… PB
-
T W S, I have no issues at all with what you are saying, as I said, this is just my personal view and preference. I’m quite sure that I’ve not even advised anyone to consider replacing these leads either, and I’ve never heard of any related problems. If you were referring to the batteries in the scale model then although there was quite a lot wiring associated with the backup unit I’d have thought that this might have been the main culprit in itself. If there were any standard diodes in there for instance, they alone are worth around a 0.6 - 07V drop, transistors the same. Schottky diode types are better, the forward voltage would be around 0.15 - 0.3V. The volts drop would have been there all the time, when the 5 cell battery was at 6 volts, the rx = 5 volts, (on load), when the battery voltage was at 5 volts, it would be virtually flat, the rx = 4 volts. At the end of the day, though, I suspect that his problem may well have been good old fashioned flat batteries anyway, no way of knowing. One of today’s telemetry systems would have been a godsend there, methinks! If anyone has one of these systems in use it may well be doing a similar check just to see what the drop actually is nowadays. Soldering the leads together fixes any connector issues. Years ago I was told by an ‘expert’ that my soldered joints were suspect and could fall apart at any moment. So I formulated my own test on said joints and I soon discovered that this was definitely not so. If fact, quite the opposite was the result. I’ve done this solder stuff a fair amount in the past, when I made my own 5 cell NiMH packs I soldered them to the switch harness. This meant they were never going to become unplugged in flight and with the added little bonus that the wires could be cut to length and therefore would help to keep the fuz tidier I also made Nicad and NiMH flight packs and I used silver loaded solder on all the new battery work; the conductivity is a little better than standard lead/tin solder. Although I’m sure in the end it didn’t really make much difference anyway, I was just a glutton for punishment. There will also be some volts drop across the motor cables too, but maybe insignificant amongst the rest of it. However, as I remarked in another post elsewhere recently, our power measurement is only a measure of the heat generated within the circuit so it’s very important to keep the resistance as low as possible anyway. PB
-
Nigel R @ 04/09/2018 14:10:37 and The Wright Stuff @ 04/09/2018 14:17:21 To answer your questions both the models and the servos are pretty much standard size, although I’d most likely upgrade the servos to digital metal geared types. For the very same reason, really, it gives me more overall confidence in the control system. As I said, I’m sure the standard type long extension lead is perfectly ok, it’s simply that I regard it as being a bit flimsy. Maybe there are heavy duty types around which would suit me be better, but by the time I’ve ordered and the postman’s delivered I can have the servos already working with my cobbled together bits and pieces. I certainly don’t have any issues with anyone that uses these either; and I guess that’s going to be a very large percent of the modellers that needs to do so; it’s just my personal preference to fix my own… PB
-
O G, My very simple take on this would be to suggest that if we double the length of a given piece of wire we double it’s resistance; if we double it’s cross sectional area we halve it’s resistance. So my equally simple rule of thumb might be - keep the wires as short and as fat as possible! But all within reason of course. It’s always struck me that the model world tends to be fairly economical with the wire sizes, understandably so, flight battery and motor wiring seems to be generally ok; and probably you can considerably overrate short lengths for short times and get away with it too, the one that I’ve never been really convinced about is the long extension servo lead. For instance, if I move the rudder and elevator servos to the back of the fuz I cut the servo lead in half and solder in a homemade extension with heavier wire cut to the right length. It’s maybe the manufacturer’s lead is ok anyway, but from a safety point of view I’m willing to accept a small amount of extra ballast just to be reasonably sure the servos are going get enough volts and therefore enough amps to faultlessly carry on performing when I really really need them to. Once upon a time a colleague took a very nice large scale model to a comp. The receiver supply was two 5 cell NiMH packs via an expensive all singing and dancing backup unit. Apparently he did a fair bit of flying during the day and then finally was asked if he would do a few circuits for the benefit of a local television crew that were there. This flight also became a bit prolonged and unfortunately before he could land the model crashed… He first thought the batteries were at fault but when I checked them they proved ok; however, when I tried the volts drop across the whole supply circuit with the two packs fairly well discharged, as would have been his case, it was ranging down to nearly a volt when moving the servos, taking the voltage at the rx momentarily down below 4. In the air the control surface loads on the servo motors would have only made this situation worse. He was instantly convinced enough to remove all the paraphernalia and just revert to a single battery saying that he would change the pack halfway through a flying day. This seems to me to be a classic case of two faults getting together at the same time, the excessive volts drop and maybe not quite enough battery capacity for unusually long flying times. But I would have also employed my very best favourite safety belt too, the on board rx voltage checker. I’m sure this would have prevented that last take off so that at least he could get a bit of charge back in the batteries first. To my mind taking off without know how much charge is in the batteries is akin to taking off without knowing how much fuel is in the tank. But at least in the fuel tank case you would still have some gliding control… Sorry for going a bit off topic there but I’m sure we can at least say that it’s just a little bit related… PB
-
How do you compare electric motors
Peter Beeney replied to Nigel Heather's topic in General Electric Flight Chat
If you do eventually decide to have a little dabble with the Easy Street II Nigel, there are some alternative motors which just might be worth having a quick butchers at such as this little gem, the Turnigy Aerodrive. This is the one that PatMc linked to first. Same price at 31 notes; size and weight too; 1 gram difference. This one has a kV of 1250, (I know, I know, but keep going!) 755 watts and a 5mm shaft. I particularly like the resistance though, at 22 milliohms that looks like good value for money. The total resistance of an electric motor power train is a bit of a Holy Grail, the lower it is the better it is! This motor also has some good reviews, I reckon it will go very well on three cells. If you were to bolt a 10 x 3 APC on to start with with I’d roughly calculate a S & L speed of 33 - 35 mph on 3S. This is now handleable for sure, even a little on the docile side perhaps. The current consumption will be low as well, most likely below 20 amps so everything will stay cold and the battery will go on forever. Well, perhaps not ever but certainly a good few minutes. If you ever fancied winding it up a few shades you can just change the prop up one pitch at the time. And indeed at the end of the day I’d consider that if you wanted to it’s still got all the potential to go all the way up to ballistic on steroids… Happy landings… PB -
How do you compare electric motors
Peter Beeney replied to Nigel Heather's topic in General Electric Flight Chat
Nigel, There is a Quantum II 25 speed model, here, that might be something else to look at. kV 1250, 50 amp continuous current, a 4 cell battery, 60A ESC and a 7 x 7 prop recommended. If this is worth anything I would check the unloaded kV with a tacho on 4 fully charged cells to make sure the plate value is correct, it usually is but certainly not always, and with this motor that should result in about 21,000 rpm. Then I’d try a 7 x 7 APC i/c prop and check the revs again. These will certainly be lower, but hopefully not too much and I’d also check the current with a clip on ammeter. After a bit of a prolonged run I’d check everything to make sure there are no hot spots. If all is ok I’d try it in the air. If this set up doesn’t really suit the Easy Street, a bit too quick maybe, then I could change the prop for say an 8 x 6 or even a 9 x 5 for roughly the same power requirements. But I’d check each time to see what was going on to make sure I’m still within all limits. Fitting a bigger prop can sometimes add to the load and hence the heating effect if I’m not careful. If the ammeter now reads 40 amps say then this is about 600 watts, which I suspect would compare fairly well with a good 2.5cc i/c engine. Although the engine power is perhaps generally more accurate because it’s power measurement figure is what the crankshaft is actually producing whereas my electrical measurement is just that of the heat produced in the whole circuit; and they don’t always amount to the same thing. If I did the same exercise with a 1,000 kV motor I would of course start with a figure of 16,800 rpm. Or 12,000 for 3 cells. 600 watts translates to around 0.8 HP. Good luck. PB -
See if you can help me with this
Peter Beeney replied to David Davis's topic in Electric Flight for Beginners
As I remember there are answers to the smaller prop conundrum back in the depths of threads past, but maybe one reason is that it’s tied up with electrical principles and the way the motor works with respect to something called the motional or back emf. Also one other important principle is the fact that if you double the voltage applied to a given resistance you quadruple the power (heat) it has to dissipate. We are not actually doubling the voltage here but we are increasing it. Applying a lighter load, or smaller prop, allows the motor to spin faster thus generating a greater back emf to oppose the applied voltage and thus the amount of heat the motor has to dissipate. This is all very simplistic but what it means is that if you still wanted to turn the larger prop at the higher revs then you may have to find a suitable (larger?) motor to do it. Considering a fictitious motor for a moment with a kV of 1000 revs per volt, an internal resistance of 50 milliohms or 0.05 ohm and a supply battery of 10 volts; that gives us an unloaded speed of 10,000rpm. Some current has to be flowing to create the magnetic field to enable the motor to run and also overcome the motor’s inertia, this is sometimes given in the spec along the lines of: Unloaded current - 1 amp at 10 volts. (Supplied). My brackets. This equals just 5 watts of heat dissipated. If this were our motor, say, then the back emf generated would be 9.95 volts, allowing just 0.05V to be applied to the motor to obtain the necessary 1 amp. If we then prop it with a smallish prop the motor will slow slightly, the back emf will then also decrease proportionally, therefore the applied voltage will increase and more current will flow to increase the torque. Crucially though, the watts generated in heat dissipated by the motor are now also staring to rise. Hang a larger prop on and and the same thing happens over again but the heat is now increasing at an even greater rate. Let us consider fitting a prop such that the back emf is reduced by one volt, now we have a rpm of 9,000. The prop has reduced the revs by 1,000. Now 1 volt would be applied to the motor and the current flowing will be 20 amps and the watts needing to be dissipated would be 20. A larger prop dropping the rpm to 8,000 will result in 2 volts being applied and 40 amps flowing; that’s a twofold increase, but the watts situation increases to 40; that’s a fourfold increase. So the heat output has already increased 4 times. Now you are getting in front of me perhaps, continue to take this down to to a point were the motor is actually stationary then the full 10 volts would be applied, 200 amps would flow but the watts have now increased to 2,000. This is all heat so hence the possible desperate smoke signals for help… If we now fictitiously add a cell to increase the the battery voltage to 15, then all the figures change. The unloaded rpm = 15,000. Now our same previous prop that reduced the back emf by 1 volt would not be able to do the same here, the total inertia that the motor has to overcome is greater so let’s say the revs reduce by 1,500. Now 1.5 volts are applied to the motor and the watts dissipated are up to 45. The larger prop requires an even more turning effort so maybe the revs are down by say 4000. Now for the same propeller the watts are up to 320. With the motor at a standstill the watts equal 4,500! That’s fifteen hundred watts greater than the ubiquitous 3kw mains heater! This is all hypothetical of course, I’ve just made these figures up to nice round numbers, but it might be some sort of an answer to the question: Why is it that when describing electric motors that suppliers recommend using a smaller propeller with higher voltage packs than they do with lower voltage batteries? This well might nicely lead us on to one other valid point as well. In theory we could go on applying a higher and higher voltage to a motor and it would just turn faster and faster. However, from the above it can be seen that eventually the effort to overcome the inertia of even the unloaded motor will be so great it would not be possible to fit any size of propeller at all. A rule of totally diminishing returns, perhaps… And this just might happen sooner rather than later, too… PB -
Chris Walby @ 28/08/2018 11:58:08 Many thanks for your reply, Chris. I remember in the first instance we were surprised, nay, rather more astounded probably, with the quality of the Assan radio and it’s shorter than short receiver aerial, but after a few other similar examples and results we accepted it as more or less the norm. Right back in the early days of 2.4 I did read that some electronics bods had tested a radio up to 1.5km still maintaining contact ok; however, again that was direct line-of-sight, anything in the way and it all went a bit blank. I’m sure I’ve always been very lucky because I seem to have had very few problems with actual radio failure, right back from the days of single channel. With the greatest respect I think if my radio started playing up as yours seems to I would want to dig into this fairly sharpish too. I have to admit I’ve never tried a low power range check, I’m sometimes a little sceptical by nature, this probably dates from way back in the days of megs rather than gigs when I found the then ‘aerial down’ short range check was by no means infallible either. There have always been anomalies, a long time friend and flying mate using Spektrum from it’s arrival on the scene together with small very fast foamies had the odd but persistent unexplained crash. This when Spektrum was a bit at the forefront of many discussions. For various reasons I was again sceptical about the BECs in many speed control units back then so eventually he shoehorned a small rx battery in all his models, (whenever possible), and connected it to the rx just to back up the BEC supply. He later remarked that it had cured all his Spektrum problems; and he still uses a backup rx battery… We do seem to have some discrepancies with the distances involved, on a good weather day we’ll try a few radios out using the same MO as you, just walk away with presumably the model on the ground and see what sort of results we get. In all honesty I’m not entirely sure about the 250 metres ground range you mention but we will have to try it before making any firm comments. Good luck with getting this sorted… PB
-
I related this story in a previous thread many moons ago; now I’m wondering if it might again be of some interest here. We do a long range occasionally because we reckon this is fairly foolproof inasmuch that we reckon that if the radio generally has satisfactory range on the ground it’s most likely be ok in the air as well. This consists of placing the rx, battery and two or three servos on a metal folding chair at the strip and then taking the tx to a point across a shallow valley 700 metres away; but still direct line-of-sight. The tx position is then very close to the corner of a small wood. If the rx is in a model it’s stood on the ground but moved around to suit. We first tried this when a colleague converted a 35 meg Futaba 9 channel tx with an Assan 2.4 ‘hack’ module. The rx aerial is just three quarters on an inch long and sticks straight out the back and we wanted to see just how good it actually was. Just to try and complicate the issue a little more we place 3 transmitters, all switched on, underneath the chair. Comms link is by mobile phone, (another possible hazard, maybe?), and the tx is then tried in every configuration, including a lot of both aerials pointing directly at each other. The rx is moved to different positions as well as the tx. Plus a quiet five minute period of no activity to check for interference from under the chair. We now consider this to be our benchmark range check. I have to say that so far this little this little strategy has always been a 100% success; and it also included a Spektrum DX5e that I bought long ago as a buddy box. And as it so happened the Assan kit behaved itself faultlessly too. As an aside I can add that I also tried the Spektrum rx in a powered glider as an example of how not to do an installation, such as servo and battery leads twisted together with the aerials, wrapped around the rx and then just bundled willy nilly into the fuz. I tried a few different combinations of this and eventually I was flying was on the limit of visibility but I never did have the slightest indication that there was anything other than than just a perfectly reliable radio link. Actually we don’t really do this stuff too much any more, I think we’ve long concluded we don’t get many incidents in the way of range or installation problems anyway. The occasional crash can invariably be explained by some other reasons, such as disorientation or power failure of some kind; but that’s a another story… However, one thing I think I may be able to say with some certainty, I suspect that if you ever find yourself flying at a distance of 700 metres with anything other than the largest of models then you may find your immediate attention could well be focused on the one of adequate vision rather than radio range… …it’s already out of sight… PB
-
Yes, indeed, I found that as standard the Riot is absolutely fine, I certainly never had any problems with servos or pushrods on three cells. It was only when upping the speed a bit did it become apparent that sometimes the controls were wondering whether to operate or not; not really an ideal situation for my blood pressure. Something had to be done. Of course it may have been simply my Riot was at fault, others may not have the same problems. I tried a test flight (2.2Ah 3 cell) in training mode down to a flat battery, this went to 14 minutes; average current consumption therefore around 9 - 10 amps; based on that for training purposes when there was a little queue of young wanna be aviators I used clockwork kitchen timers set to 5 minutes and ran 2 flights per battery. At one time we had some short flight problems which I initially thought was battery but it was an ESC. Century replaced it immediately. I simply check the motor’s unloaded speed, usually very close to quoted figure but some can be way off and then try different props until I find the best one to suit the conditions I want. It might then be possible to find the watts/lb by going backwards perhaps. My clamp meter is a bit versatile, it’s auto AC/DC measuring amps, watts, V/As, phase angle, volts and Hertz. It also has a connection to drive a scope; but I’ve never bothered with any of this, as long as the prop turns at a point fairly close to the unloaded speed and nothing much starts heating up under full load that does it for me. A bit of guessing here. Riot flying weight? 3lb? Full chat current on 3 cells with a nominal 11.1V? 30 amps? If this is anywhere near then I’m thinking the watts/lb are around 110. Sounds about right to me. Guessing again, I’d say the Ruckus as listed on 4S at 40 amps is very close to around 150 - 160 watts/lb It keeps that charger warm, at least… Happy landings.. PB
-
Geoff, Apologies for going slightly off topic but this might at least partly relate to the Ruckus; I changed the prop on a Riot for an APC i/c 9 x 6 when I went to 4 cells and the result was instantly electrifying. (Sorry!) But I notice the motor is now V2, version 2? so it may be completely different. Certainly worth investigating though. This from a Riot thread that I posted in 2016. I have a ‘hack’ Riot which has flown on 4 cells for quite some time now. It’s certainly been through the wars, so to speak, but still keeps tramping on, actually it’s still rather lively; and it’s also been modified a bit to cope with the extra poke. The motor is ok, but it is fairly basic, it has a plain oilite bronze bush bearing, they are not that easy to repair but I’ve vandalised mine more than once; and oddly enough, I can find every size of bush on the web except that one. Same with the rear end circlip, we have a very friendly motor accessory shop handy and they have every size of E clip bar the Riot motor! There is a compatible ‘Donkey’ motor from HK, exact same fit and very much cheaper; lower kV rating, though, 720 from memory. So a 9 x 7 might be ok here. When I changed to 4 cells I straightaway found the rudder and particularly the elevator were very iffy, so I decided that the push rods were now not up to the job and I moved the servos to the rear end and used short stout metal push rods. Much better, but the elevator could still be a bit reluctant, especially at the end of a flat out power dive very close to the ground. Interesting times! Installing a Blue Bird 380 metal geared fixed it, now total confidence in any situation. The aileron servos have never blinked, though, despite having the max travel available. Like every thing else, they often have to work hard when I go flying, I sometimes tend to get a bit carried away in the heat of the moment… I changed straight to a 9 x 7 ACP i/c prop, this was excellent until the motor started chattering loudly, on landing I found the bearing had knocked itself out and was mostly plastered around the motor on the inside of the fuz in the form of a black gunge. I replaced this with one from a motor with broken lugs, changed to a 9 x 6 ACP and it’s been fine ever since. I’m not too keen on the Century prop driver either, so I changed that too. I tend not to generally consider watts and stuff too much, I just use a tacho and check how hot it’s running. Incidentally, if the motor starts stuttering cut the throttle immediately; the power system is being subjected to a full current flow and could quickly complain by rapidly overheating. The motor is rated at 850 kV and 4 cells fully charged = 16.8V. 850 x 16.8 = 14280 rpm, which is about what I clocked for the no-load rpm. On the 9 x 6 it’s 12000 rpm, which gives a theoretical in the air speed of about 68 mph. The nominal voltage figure of 14.8 gives a speed of about 60 mph. The pack is a 2.2Ah Nano Tech, I fly for around 5 - 6 minutes if using a lot of loud pedal, but there’s always some ampere minutes left. I’d estimate a current flow of around 30 amps, perhaps, everything stays nicely cool even after a lively flight; but there is a good cooling air flow through; very important. The next move might be upping the ante to some Hyperion higher voltage 4 cell packs. A little bit more get up and go and these have a reputation for being able to hold the voltage up under load, too. Hope this useful for anyone who is looking to improve the performance a few shades! Edit. Just for interest, I’ve just checked the current, and with a fully charged pack it’s 33.3 amps. So up to about 560 watts then. PB As I recall the standard model came supplied with a black plastic 12 x 6 prop which was ok for normal flying. Circa. 2012 onwards we had 3 Riots plus some other models at a school where I was then helping some beginners. If the Ruckus is as tough and as hardy as the Riot it should be another winner. As always I just tend to poke and hope. But I’m sure for more refined modellers that would be trial and error… I never did check the CoG but moving the servos to the back increased the agility too. Great stuff! PB
-
Mike, Thanks for your answer but after some considerable tinkering with this stuff quite a while back I found there was little or no evidence to suggest any real issues, at least as far as I was concerned. For instance, in practise I found it actually quite difficult to charge a 4 cell nickel battery at all with a 5V regulator, as soon as the pack is at the 5 volt level (quite quickly) everything stops. The regulator is current limited and thermal protected too; I consider the thermal switch might just be the ‘destructive little gremlin’ I previously mentioned; it protects the regulator just fine but can easily destroy your model in the process! Previously the fact that I was using a battery/BEC combo for rx power saved my bacon on two occasions. Flying a ‘hot-liner’ powered glider the motor battery went open circuit, most likely due to over exuberant use of the throttle stick. I was still able to land safely but without the receiver battery this would have been a missile with no means of control, something that I personally believe to be a very dangerous (and often unnecessary!) situation. It also allowed me to do all pre-flight checks before connecting the motor battery in relative tranquility; a 16 x 13 carbon folder turning at around 10k is definitely more than just a bit intimidating when close up; I treated it with more care than I would a demented chainsaw on steroids! Yet another extremely worthwhile safety point in my opinion; taking off with the ailerons reversed is still a trick that can occasionally be observed. Of course, it would still be possible to do all this stuff with the pos. wire disconnected and no motor battery, this is just another case for having a separate rx battery supply I take the point about the switching regulator but I’ve not used one so far I know, I’ll see if I can find one to play with. With regard to inadvertently opening the throttle, for many years now I’ve assigned a transmitter switch to prevent the throttle opening. I call it ‘throttle lock’. Also helps considerably with the intimidation bit. It would also prevent an inadvertent start up relating to the BEC running the motor too. I’ve found that if I always work to a set procedure when flying it does help to prevent mistakes because actions tend to become automatic but I’d also admit that I can go well off the track on occasions. I have proved that more than once!! Nothing is ever guaranteed but I do try to take every precaution. So in my semi-conscious risk assessment mode I’ve still decided that the parallel BEC/battery set up is perhaps just the lesser of two evils, as they say. Regards. PB
-
As a small aside to the main question within this thread, I notice there is still a continued reference to it being of some importance to disconnect the red wire in the throttle cable from the ESC when also connecting a battery in parallel to the receiver. I think this also sometimes applies when paralleling two ESCs together. Solely in my opinion this is a bit of a wrinkled old conker that’s been knocked about a bit over many threads in the past and has taken a few hits but as far as I know has never been mortally wounded; or even particularly scratched when push comes to shove. My thinking is that this actually doesn’t matter either way, really, the ESC will function perfectly ok with the wire connected or disconnected; the internal operating conditions do change though, but that is all unseen of course. In fact it may well be that there is some sort of argument for saying that adding a battery is the answer to a problem, as in Joe’s case. He disconnected the red wire perhaps but it would not have mattered had he not done so; in my view this is rather an infrequent and unusual and situation, though, I’ve never seen this happen, and I’d be endeavouring to find the root cause in the first instance; this could perhaps be a type of fault which might eventually become a disaster… And it not be the first time that’s it’s happened, either. Long ago I related a story of how disconnecting such a battery ultimately resulted in a total matchwood type crash; and to initially confuse the issue even more so the radio was working perfectly afterwards; and that destructive little gremlin has also appeared out of the blue on more than one or three occasions in the past, too… Just an individual preference, I guess, in such circumstances I would want to keep the positive supply connected but others may well decide to remove it; and in 999 cases of a 1000 it’s always going to go entirely unnoticed either way… This is all definitely just my own personal viewpoint and not in any way meant as any form of instruction or advice etc. PB
-
Joe With hindsight I now think it might have been rather more straightforward (and easier!) to do a spot of backtracking and then simply ask - ‘Did you by chance happen to use the same ESC?’ If not it then seems to me it’s beginning to stretch a coincidence a little bit more than somewhat… See here PB
-
Joe This sounds to me as though this may possibly be an electrical supply problem from the BEC. Assuming that in the first instance you are using the BEC supply via the throttle control cable, (normal practise), when you move the servos a resulting volt drop - for whatever reason - is seen at the receiver causing the throttle channel to mis-operate and momentarily fire up the motor. If this is so it might be a fairly serious condition and perhaps needs a spot of looking at. Connecting a battery to the rx then immediately provides a robust parallel supply which won’t be affected by the sudden current pulses caused by the servo motors starting up when you operate the sticks. Thus the rx supply voltage remains stable throughout and ensures the throttle doesn’t operate. On the other hand it might also be the case that these same pulses are causing the voltage regulator (BEC) itself on the ESC to fluctuate and so affecting the components on the ESC. Connecting a battery would have the same effect as before; it would keep the voltage constant. But this is pretty unlikely I’d have thought however, that might point to the regulator being seriously under-spec. BECs are usually at least 2 - 3 amps output these days. If you don’t have any test equipment, voltmeter etc., then one answer maybe is to simply leave the flight battery connected anyway… Good luck. PB
-
Motor + ESC Timing and frequency
Peter Beeney replied to Gary Murphy 1's topic in General Electric Flight Chat
Gary, My take on both the timing aspect and the frequency of brushless motors is that as far as aeromodellers are concerned they are both relatively unimportant; it’s perhaps only when you are looking for the optimum performance that adjusting the timing can make the difference. However, as with just about everything else in life, it has to be at least a small compromise, so some care is needed, altering the one condition may result in other unwanted effects. As you say, you can change the ESC setting to suit but I think it’s most unlikely you will be able to change the frequency. Indeed, I’m not sure that you would ever want to change it. 5 degrees of timing is low, is your motor a low pole count high kV lump? Some ESCs have an auto timing setting, this may give you the best all round performance; no harm in trying. I suspect the 8KHz frequency figure may suggest that this is the lowest to use, or perhaps it’s to do with the resonant frequency of the motor; either way I’m sure I wouldn’t be poggering over this too much. A name/description for the combo would be very useful… The frequency is always in the background, this is the speed at which the Pulse Width Modulation, (PWM), signal is being generated within the ESC to regulate the voltage, (and thus the speed), being applied to the motor. This switches the current on and off in a series of equal length pluses, with the on/off time variable in each pulse.This pulse train can tend to raise the temperature on the ESC, though. When the motor is on full chat it’s getting all the available battery voltage so there is no modulating signal present. These oscillators are usually graded in steps of 2KHz; 4KHz; 8KHz; 16KHz and so on; 16KHz is a popular ESC figure but your’s may well be an exception to the rule. But again, all this is of little consequence anyway… Hope this is of some use and as stated, these are just my own views and ideas, they may not all be correct so I will apologise for any mistakes made in advance. PB -
It’s always seemed to me that whilst great acclaim is made for all these aeroplanes, and rightly so of course, occasionally there maybe some scope for giving rather more credit to the men whose ideas led to these aeroplanes in the first instance. Clever men with long range forward vision. The Mosquito was a good case in question; Geoffrey de Havilland and his team designed it and Wilfrid Freeman ensured that ultimately it was built and went into service. Although this did require some considerable tenacity to achieve on their part however, because reading between the lines of many of the wartime history chronicles there was much infighting at times between various departments and personalities. Nothing changes much, even in wartime. To start with Geoffrey de Havilland had to fund it himself as a PV (Private Venture) right up until the first orders were placed. Wilfrid Freeman also had enough faith in the project to ignore orders from Lord Beaverbrook to cease work on the development of the Mosquito at least three times; it also seems as though some others weren’t convinced either; indeed, for a while the embryo plane was known as Freeman’s Folly… However, once they started flying in earnest they soon proved their worth. For at least the first eighteen months they were the fastest planes in the air; at least until the later variants of the Focke Wulf 190 began to play catch-up. They went on to prove that they could deliver bombs at very long range with pin point accuracy for the lowest loss rate in Bomber Command. They’ve also been credited with being the most successful photo reconnaissance vehicle ever. And that’s from more than one source, I believe. I remember reading somewhere too, a little story about Geoffrey de Havilland in the early days visiting an American Airbase to give a ‘spirited demonstration!’ in a Mossie. Unfortunately the article didn’t describe too many of the manoeuvres that he performed but it did mention vertical upward rolls from ground level on one engine… Doubtful if there’s any film record, and perhaps even the Yanks were rendered speechless for a while… Maybe Bob Hoover was watching… Today’s H&S inspectors would still be having nightmares… Much later on a 12 foot long 57mm 25 round rapid fire Molins cannon was slotted into a few Mossies and used as submarine hunters in the Bay of Biscay; which they did with great aplomb… So from starting with no armament at all right up to becoming a flying howitzer and all the time performing as a high performance bomber and aerial camera cab in between… An extremely efficient and versatile aeroplane if ever there was one! Sir Geoffrey de Havilland and Air Chief Marshall Sir Wilfrid Freeman were both giants in their own fields. The author Anthony Furse describes Wilfrid Freeman as The Genius behind Allied Survival and Air Supremacy, 1939 to 1945; …and that all sounds about right to me. Wilfrid Freeman had an interest in the development of the Merlin but the Mustang was also one of his favourites. He submitted the original spec. to North American Aviation, fortunately the president there, one J. H. ‘Dutch’ Kindelberger, also had his eye on the situation in Europe and could see what was happening; he’d had already done some ground work in anticipation and thus was able to get a prototype ready quite quickly; more forward vision again. The first Mustangs arrived at Liverpool in November 1941 and one soon found it’s way to Duxford where Wing Commander Ian Campbell-Orde, CO Air Fighting Development Unit (AFDU) immediately rang Ronald Harker giving him an opportunity to come and fly it. Ronnie Harker was a Rolls-Royce service liaison pilot at the RR Experimental Flight Test Establishment at Hucknall, he flew as a test pilot in an evaluation and troubleshooting capacity, particular on the Merlin engined planes, but with a sideline in flying all their competitors and other brands that he could get his hands on as well, including enemy types if they became available. Mr Harker was suitably impressed with the Mustang, in his subsequent report he included the paragraph - ‘The point which strikes me is that with a good and powerful engine like the Merlin 61, it’s performance should be outstanding, as it is 35 m.p.h. faster than the Spitfire V at roughly the same power.’ This quickly went up the line to reach the ear of Wilfrid Freeman and thus the rest, as they say, is history. The Mustang was originally designated the NA-73, the Americans went on to name it the Apache but the RAF decided it was a thoroughbred Mustang; the Americans then fell into line with this. I’ve no evidence of course, but I’ve always liked to have had a little suspicion that Air Chief Marshall Sir Wilfrid Rhodes Freeman, 1st Baronet, GCB, DSO, MC, FRAeS might just have had a small input in this minor but very appropriate detail too… PB
-
Apologies if slightly off topic There is also the ‘semi-legitimate’ type of scam which can can exist without you actually being fully aware of it it. It seems money can extracted from your bank account without necessarily your having given your full approval……or even any conscious approval at all! Some years ago quite fortuitously I noticed a withdrawal of £15 from my account; it just happened to be the last entry on a mini-statement. I couldn’t remember doing this this and it started to irritate me so fortunately I went in a bit deeper. The online statement just showed it as being identified only by a long string of digits, when I googled that it was just a single web page which I didn’t recognise at all. Looking back at the statements it was there on the previous one again but no others. I took it to our local bank, a small rural branch because they are very helpful indeed, the young lady said “ That certainly looks suspicious”, she picked up a phone, dialled a number and said “ Have a word with the bank’s fraud squad”. The gentleman I spoke to was not quite so accommodating, he just said it wasn’t fraud because it was a legitimate company. I asked what it was about and it was apparently an outfit which gave out information, email or hard copy, about ‘monthly best buy’ bargains of all sorts of items, in the nature of the monthly mag ‘Which’, perhaps. The first three months were free and after that, if you didn’t cancel, you just continued to pay the £15 monthly subscription ad-infinitum. I stated that I’d never signed up for this and I’d certainly never received any such information. I also very much wanted to know how they’d managed to set up the direct debit without my knowledge or permission. His rely was a trifle less than reassuring: “Oh, there are various ways, but you probably bought something online and didn’t un-tick a box as an option at the checkout! All quite legal!” So I presume this must have been in the very small print somewhere. He did particularly name one country wide store, the one were you write numbers on a slip of paper and the goods follow back over the counter a few minutes later. He then gave me a number to ring to cancel and get a refund, He said if that didn’t happen to get back to him. I did this, spoke a very foreign gentleman who did the necessary after a short halfhearted discussion not to leave. The £30 was back in straightaway. After some more Google time I found this was very widespread malaise indeed, worldwide in fact. Mine was one of least worse cases, I remember one American victim said that he and his wife had a very busy joint account and this mob had been lifting $10 a month for nothing for several years before they latched on. He didn’t say if he’d got his money back, though. I also noticed that the same country wide retail store got the occasional mention as well. I very much suspect this ‘approved fraud’ is still in existence. If it weren’t untouchable I’d have thought it would have been shut down; and perhaps it might be off shore too, that might make all the difference. I wonder just how many people have one of these everlasting hidden money sinks without realising it… I have read that the perfect con is the one that you don’t know is happening; sounds about right; I guess I got lucky at the time. But even now I still pay fairly close attention to the mini-statement… and all the small print... Yo’ll be careful out there now… PB
-
Understanding Watt Meters
Peter Beeney replied to Mike Downs's topic in Electric Flight for Beginners
Exactly so, Mike, but I’m still a little sceptical in parts. Multiplying the amps by the generated voltage to get the output power is surely just measuring the heat generated again, not the mechanical turning force? This may well be ok when the input and output power ratings are as close together as they are going to get, but not so accurate when they are far apart. Your 9V example in the last paragraph, as apposed to the previous 10V, would appear to show the way this is developing. You have the ability to do the calculations so you would be well aware of whats what but I might simply look at the 387 watts displayed on my watt meter and think what a nice powerful motor I’ve got; this is exactly the reason why I’m saying I would be a bit cautious when comparing figures. Also the sentence: ‘The motor is also measured to by running at 10,000 rpm,’ does that imply you’ve also clocked the rpm with a tachometer? If so, how often is this action quoted, recommended or even mentioned? I seem to have missed it. As it happens, a tacho is always right on the top tray of my toolbox together with a new CR 2025 cell, it’s bound to go flat just when I need it…I’ve found with a bit of practise this can give me a great deal of information. Frank, I think I would like to try out the bits and pieces listed in Mike Downs’s OP on the bench for myself. For instance, what (low) cell count pack would I be using to keep the amps at 50 or below on a 12 x 8 prop? Also what are the revs, this is where I start, it will give me a good indication how the model will fly amongst other things. Mike B mentioned his ‘good’ 12 volt battery, (able to sustain 12v under that sort of load!), I use a fully charged 12V car battery for bench testing motors, now that is a nice stable supply! If I had a model that required a larger slower propeller I’d want to obtain an appropriate motor that still allows me to use it at it’s optimum revolutions point. Nigel, I’m not sure a propeller is any sort of dynamometer at all, but with a bit of trial and error, or as in my case, poke and hope, it will give you a fairish visual indication of how well or not your model will perform. At the end of the day I probably don’t really need to know very much information at all, I can just tinker until I get it right. But a dynamo. will give me the point on the revolutions curve where it’s at it’s most powerful straightaway. Interestingly, I believe that model aero engines were once tested with a propeller. They needed to know the torque so that together with the rpm they could calculate the horsepower. In the first instance they bolted the engine on a torque beam which was variably weighted at one end and pivoted against the opposite torque of the propeller thrust; but there were some anomalies arising due to the prop wash etc. so they found the the dynamometer a better instrument to use. And somewhere in the distant memory banks I’m sure I’ve seen a picture of an early full size aero engine up to the same sort of caper… I simply said that I would be a bit cautious when directly comparing the output power of the battery with the output power of the motor; and also including i/c. That’s not to say you shouldn’t do it though, in fact I tend to subconsciously compare electric motors with i/c all the time, I suppose because I’ve used glow engines for so long I’ve a pretty good idea how they are going to perform. Again fine if the the electric set up is spot on but again if the watt meter gives an erroneously high reading it might be a tad misleading. However, I’m sure that as folks are using e.p. more and more the increasing knowledge and experience will lead to less confusion. I actually think the modern DC brushless motor is a real cracking lump of engineering. With it’s design features and some help from components like neodymium magnets and the very essential but equally as impressive Electronic Switching Commutator it’s a real little powerhouse; and I have noted at the patch that some are still running faultlessly after very much use, too, so in some cases at least their longevity would appear not to be questionable either. More power to your (electric) prop… PB -
Understanding Watt Meters
Peter Beeney replied to Mike Downs's topic in Electric Flight for Beginners
I think I would always be a bit cautious when it comes to directly comparing the output power of the battery with the output power of the motor; or indeed the output power of an i.c. engine, too. To my mind we are measuring two different types of movement here. I’ve probably got all this wrong again, I usually seem so to do, but as I see it the battery power measurement is electrical whilst the motor power measurement is a mechanical one. They are always going to equal each other in total, but the two different effects are not always what we really want. Generally speaking,* when a current passes through a conductor it has to overcome the resistance, an action which produces heat, and it at the same time it creates a magnetic field surrounding the conductor. Again, rightly or wrongly, I figure that the magnetic field comes for free; the cost, in our case here anyway, is that it always requires it’s accompanying current and that in turn is causing heat which we don’t want, at least in this case. The circular motion of our permanent magnet DC brushless motor relies solely on the reaction, or rather a deflecting action, of two magnetic fields, one established by the flow of current. The mechanical movement, or power, of the prop shaft is derived by multiplying the torque by the rpm and here we seem to be measuring the strength of the inter-action between the magnetic fields; to get an accurate measurement of the power we would need a dynamometer to read the torque and rpm to calculate the power; whereas placing a watt meter between the battery and ESC measures the amps and volts to give the watts. Unfortunately this is just measuring the heat generated, rather than the turning motion! To illustrate this let’s consider two points on the motor’s power curve. At the instant of start up the motor is stationary therefore the current flow will be at a maximum. If we were able to read our meters in slow motion the watt meter would read max amps, therefore max watts input (all heating effect) but although the dynamometer would read max torque there are no revolutions which equals zero power output; but of course this situation doesn’t last very long; the motor very quickly starts to turn, the current flow diminishes and the speed and current flow equalise at whatever values they ultimately reach. Right at the other end of the curve let’s consider the motor in a stalled state after running. Exactly the same situation, max watt meter reading into the ESC and motor windings but no power indicated by the dynamometer, again because there are no rpm’s. As before we are just seeing the heating effect, this time possibly indicated by the distress signals given by the power train in the form of an arising column of white smoke or worse. In my view these are the two extreme points and somewhere in between there is one point where the motor will run at it’s ‘best case’ compromise speed, where the two measurements are closest together. I suspect, in very general terms, this is most likely to be not too far away from the unloaded speed, but there are many different cases. For me this is an indicator of the importance of the resistance, or rather lack of it, of the total power train. Looking at a fictitious case of 3 circuits, with 3 different total resistances but the same 10 amps flowing in each, a) 1ohm, b) 0.1ohm and c) 0.01ohm; Then in circuit a) there would be 100 watts dissipated as heat, circuit b) 10W dissipated and circuit c) 1W. All hypothetical of course, to maintain 100 amps three different voltages would have to be applied, from a) 10V, b) 1V and down to c) 0.1V. But the magnetic field strength would be the same in each case so the mechanical power output would not change. I’d judge the quality a power train by the value of it’s (low) resistance and by the same token I’d always try and keep the rpm as high as possible, within the required performance envelope of course. * When some conductors are ‘super cooled’, that’s frozen down to near absolute zero, they tend to lose their resistance. In this state a vast amount of electricity could flow unimpeded, there is no heat generated by this but a very strong magnetic field could be created. This can be used to an advantage, indeed I believe I’ve read somewhere that the Large Hadron Collider at Cern uses super cooled electro magnets in the particle accelerator. I know nothing about it, though, does it also make it cheap(er)? to run, too? But I reckon one prevailing caveat at least must be the fountain-like eye watering cost of maintaining the low low low temperature… Just my idea on the subject and of course it does not take into consideration the other principles that enable the motor to function…and no assurances that any of this is correct, either… PB