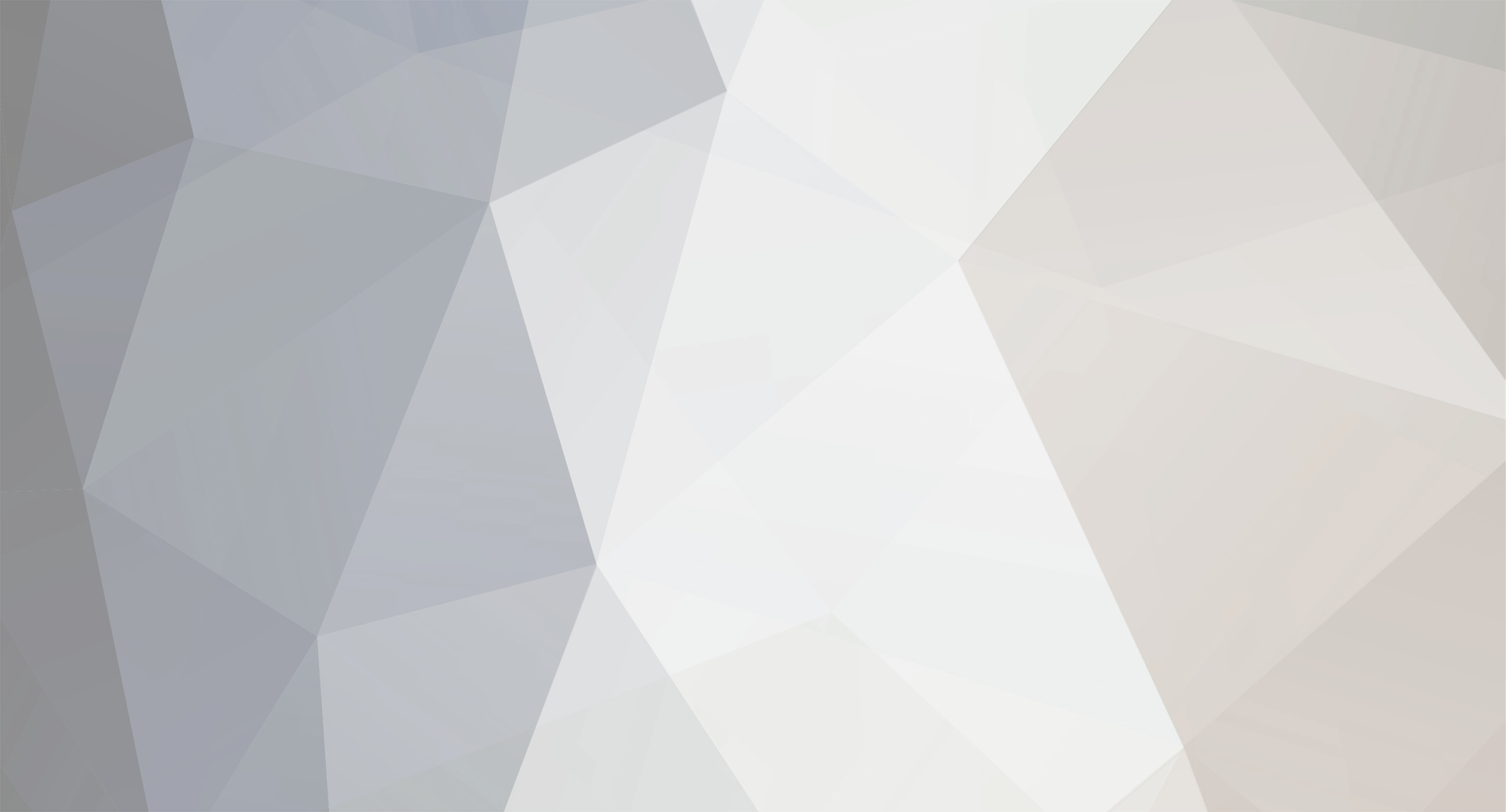
John Olsen 1
Members-
Posts
469 -
Joined
-
Last visited
Never
Recent Profile Visitors
The recent visitors block is disabled and is not being shown to other users.
John Olsen 1's Achievements
0
Reputation
-
John Olsen 1 joined the community
-
Even Experienced Modellers Can Make Beginners' Mistakes.
John Olsen 1 replied to David Davis's topic in Incident Reports
I've had the fin fall off on a Great Planes 40 size Stik. The root cause is that the bottom edge of the fin that goes into the fuselage has the grain running fore and aft, so that the balsa is being stressed across grain. The bits of vertical grain on the leading and training edge don't engage significantly with the slot in the fuselage, so it is very weak...but not obviously so unless you are looking at one with all the covering stripped off. They really need some reinforcement in this area, which I have done using bits of kebab stick for dowels. Other than that weakness, they are a good plane and fly well. John -
Just for interest, take a close look at the actual break. Quite often you will find that part of the break is smooth, perhaps with a faint pattern like tree growth rings, while the other part is rough, looking almost crystalline. What happens is that a tiny crack starts, perhaps from a scratch. With each reversal of load, the crack grows a little. With a crankpin, the load reverses every cycle. Eventually the crack is big enough that the rest of the metal fails abruptly, giving the rough break. When the crankpin on my AM15 failed many years ago, that was exactly what the break looked like. It does not help that there is a stress concentration in the corner, and it is kind of hard to design a crankshaft that does not have such a stress concentration, although there is usually a radius there to help with that. But to some degree, if it was strong enough to never break, it would be too heavy. For a given loading, there is a critical crack length, beyond which the crack propagates through the material at the speed of sound, so the final failure is very sudden. Also corrosion will both help such a crack get started, and help it to grow once it has started. On the other hand, if the engine was too lean and did a backfire, it might have managed to put enough stress on the pun to just bust it outright. A crack growing is not exactly the same as fatigue, although the effect is similar. (eg failure after some time in operation.) But metals that are prone to fatigue will fail even without an initiating scratch. The repeated cycles of loading are able to alter the crystal structure so that eventually the piece fails under a much lower load than it could withstand when new. John
-
While the Russians would like to blame the whole thing on the Mirage, the fact remains that the Tupelov broke up in mid air, without having actually collided with anything else. Should an aircraft that can fly at over Mach 1 be structurally weak enough to break up at a much lower speed when manoeuvering? It is now known that much of the airframe was made by milling from large slabs of aluminium, and apparently these were prone to developing cracks. This was one of the reasons that they were eventually withdrawn from service. Milling parts from solid is a process that is used in aircraft, but you have to be able to produce large slabs without flaws. The talk of spying is much over rated. No doubt the Russians did gather as much information as they could, but despite the external similarities, the internal design, particularly the structure, was quite different. The external shape is pretty much determined by the aerodynamics. Even with subsonic designs, all large passenger transports tend to look much the same, apart from earlier experiments with putting engines in different places. Even if they had a full set of drawings, the different production facilities and the different sources of parts would require a major redesign anyway. If you look around on Utube there are some good videos about all this. One of the Russian guys said that they were actually about 15 to 20 years ahead of having the capability to design and build such an aircraft successfully. John
-
ESM do a large scale Dornier 335. I have one, but I have not finished putting it together yet. I also have the little foamy one which goes well, although it is very easy to lose orientation with it. Currently needs some repairs! There were also some German guys producing a kit with a shaft drive to the rear propeller, as per the original, so the rear engine goes in the right place. Good idea so long as the engineering of the shaft is up to the job. The ESM one can either have a single petrol engine up front, or a pair of engines. Mine has a 160 twin up front and a 120 single down the back. Apparently as a model they fly well, without the usual problems associated with warbirds. John
-
Mixing brushless motors, ESCs with water!
John Olsen 1 replied to Delta Foxtrot's topic in General Electric Flight Chat
Actually the ideal shape of a marine prop depends on the speed and torque of the power plant, as well as the available space. Usually boats are quite limited in the diameter that can be accommodated, due to the maximum draft that is acceptable. So to accept the required power, the blade area has to be quite large, and they often have to be run quite fast as well. This leads to cavitation problems, so the blades are kept quite thin. If the space is available, a shape more like an aeroplane propeller will actually give more efficient results. However the speed has to be low enough to keep the tip speed reasonable. One form of power where this applies is with small steam plants. Steam engines usually run quite slow...my own engine is considered a high speed one as it runs up to about 600 rpm. The propeller I need to make for it will be 21 inches diameter and 21 inches pitch, and will look more like an aeroplane propeller than the usual boat type. It will have two blades. Note though that it will only be absorbing about 10 hp, which should, all going well, push the boat along at about 7 or 8 knots. This is actually about as fast as the hull would go, since this is a displacement hull, not a planing one. (The hull is 30 feet long) I think in fact a human powered boat would have similar requirements....the power plant is capable of good torque but only at low rpm. To get the best out of it, you want a large diameter high aspect ratio propeller, turning at low speed. But of course, said propeller must be fully submerged and also must not be touching the bottom of the water, so the maximum diameter may be limited. There isn't enough power to plane, so a long displacement hull will minimise wave drag and give the best performance for the limited power. (that is also why rowing eights are so long.) Even on aircraft, where possible we would use a larger propeller turning at a lower speed if we want high efficiency. However we must often sacrifice efficiency for practical concerns like not having a grasshopper like undercarriage. We can't turn a large propeller fast or the tips will exceed the speed of sound. In order to absorb more power in a limited diameter, we add more blades, although this leads to interference like on a biplane, and so reduces efficiency. John -
XT60 connectors...
John Olsen 1 replied to Tony Harrison 2's topic in Building from Traditional Kits and Plans
While we are talking about XT60, I found recently that Hobbyking is selling a little tool plus some plastic bits that make it much easier to unplug XT60 in a hurry. You install a little U shaped piece of plastic onto the male and female parts of the connector, then when you want to unplug you slip on a little plastic plier device and squeeze it, and it pulls them apart without wrenching on the wiring at either end. Seems quite a good idea to me, although ideally the bit you have to add on should have been part of the connector in the first place. You could of course also do the same sort of thing by drilling holes in a suitable spot in the connector and then using outside circlip pliers to open them apart. John -
I wouldn't have said that big ones are necessarily any harder to make. The parts tend to be larger and less easily damaged in making them. Back in the sixties, when I built my 7 foot wingspan Powerhouse, I noticed that it actually had the same number of wing ribs as the Tomboy model that was then popular with my clubmates. The Powerhouse fuselage was not much more complicated either. It certainly flew better and was much easier to trim. Small changes make a much bigger difference on a small model. With radio control, the small ones tend to be much twitchier as the time constants are much shorter. One effect of the low Reynolds number on small slow aerofoils is that the flow separates much earlier. The result of this is that the aerofoil does not behave anything like the predictions. We used to see turbulators used on free flight duration models, the theory being that it was better to ensure the flow was turbulent, and therefore more predictable, then to try vainly to keep it laminar. But these days we mostly have radio, and if we want a small twitchy model to behave better we can put in a stabiliser to make it behave a little better. I think this is good, since if you are limited in space for building or transport, you can build a smaller model and still have it perform really well. John
-
Restoring a Hobby King Slow Stick
John Olsen 1 replied to Simon Chaddock's topic in Build Blogs and Kit Reviews
I have one of these. It flies quite well although it prefers really calm conditions. Would be fun indoors in a large enough hall. I don't think the electronics would be that critical so you should be able to find something cheap that will do. Mine has been known to drop the undercarriage out in flight, but it flew fine without it. It just relies on the spring of the wire gripping in the slot. I found that I could only easily get a slightly bigger battery than specified, but that worked out fine since the battery is well forward to get the right CoG anyway...no lead needed. John -
Hi again, Try **LINK** You might find it takes a couple of tries to lap a piston to fit the cylinder, but a few extra pistons is not a big deal. I still have a model I built when I was about 14, and it flies again too. I didn't build the engine but I did convert it to spark ignition. John
-
Hi Percy Whereabouts in NZ are you? I could put you in touch with a guy here in Cambridge (NZ) who has built a number of model aero engines and is currently working on a 12 cylinder blown two stroke...I forget the capacity but it is about 8 or so inches long...there is a thread on the Model Engineer website with photos. Anything that he can't tell you about lapping probably doesn't matter. I also know some guys in Auckland who could help out with small quantities of casting sand. Another possibility these days is to draw it up as a 3D model and 3D print the wax...which can be done for you...then have a lost wax casting made. One of the members of the Auckland Model Engineers has been doing this. This gives very high quality castings. John
-
My son has the Balsa USA version of a Taube, in the smaller size. (60 size engine) That one does not have ailerons, while their larger one does. I had some correspondence with them at the time we built it, and they feel that the ailerons are not actually necessary. This seems to be born out by the way it flies, the rudder puts a bank on very effectively. Although it is obviously not an aerobatic aircraft, it is very pleasant to fly. Remember that the full size would not have been doing aileron rolls either! If you want to be really authentic, you could build it with a more scale like structure and include the wing warping. John
-
Hi Tony, That looks quite promising, provided you use it with the correct type of motor...it is quite a different type to the ones here in NZ, but I guess must be common enough over there. You will of course need to pay attention to mechanical and electrical safety if you put together something like that. John
-
Most of the smaller devices that have speed control, like drills, sewing machines etc have universal type motors in them. There is nothing to stop you using a motor of this type, although they might be at the low end of the power range that you want, and not all are meant for continuous operation. A drill for example might not take kindly to being run continuously. Universal motors can be speed controlled with a relatively simple controller. Washing machines are another story....Fisher and Paykel here in NZ pioneered the use of a permanent magnet three phase inverter motor in washing machines. This makes the whole thing a close cousin of the type of thing we are using in model planes these days, but a bit larger. (Not necessarily more powerful!) The earlier motor was similar in appearance to a normal style of mains motor with a belt drive but the later ones are a multipole machine with direct drive to the washing machine drum. They are very popular with the self sufficiency guys as they make an ideal alternator for a windmill to drive, since they can generate at quite a low speed. As a motor, they can run very slow for the washing cycle and very fast for the spin. They would be ideal for what you want except you would still need a VFD, or else enough electronic knowledge to repurpose the inverter from the machine...which would not be easy. You might look out for information on rock tumblers..they are a bit smaller but have similar speed requirements. I wonder myself if just having a couple of pulley sizes on a countershaft would provide enough speed variation. That would allow the use of a simple motor salvaged from a washer or drier. You would have to stop to change speed but I can't see that being too much of a problem. Are the alpacas good eating? I suppose there are quite a lot of neck chops. John
-
So...I had a 40 size Great Planes Stick with a 60 sized electric plant. It went really well until I muffed up the recovery from inverted flight and broke it. So I got another and powered it the same. Then I got to looking at the remains. I rebuilt the smashed wing half, and put a nacelle on each wing and powered it with a pair of 30 sized electric motors. The maiden was really promising, until the rudder and fin failed. I think the sequence was that the rudder split just above the horn, then fluttered until it broke the fin away, just when I nearly had it down. Damage was not too bad and it is nearly ready to try again, this time with improved rudder and fin, which I would say is a bit of a weak point in the original design. The rudder has the grain going the wrong way, and the piece of the fin that glues into the slot in the fuselage also has the grain going long ways, so it is not very strong. Both can easily be improved with a few cocktail sticks glued into holes. I know other people have built twin engined Sticks, so I don't claim originality, but it would be the most radical mod I have done. An overpowered Stick, whether twin or single engine, is a lot of fun to fly. John
-
The usual VFD (Variable Frequency Drive) is meant for three phase motors. They are not too expensive these days but you do need a three phase motor. If you are buying a motor new a three phase one is likely to be no dearer and quite probably cheaper than a single phase one, but of course you are not so likely to be able to salvage one out of an old washing machine. You may be able to get one from the sort of place that sells second hand machine tools or even from a computer scrap outfit. John