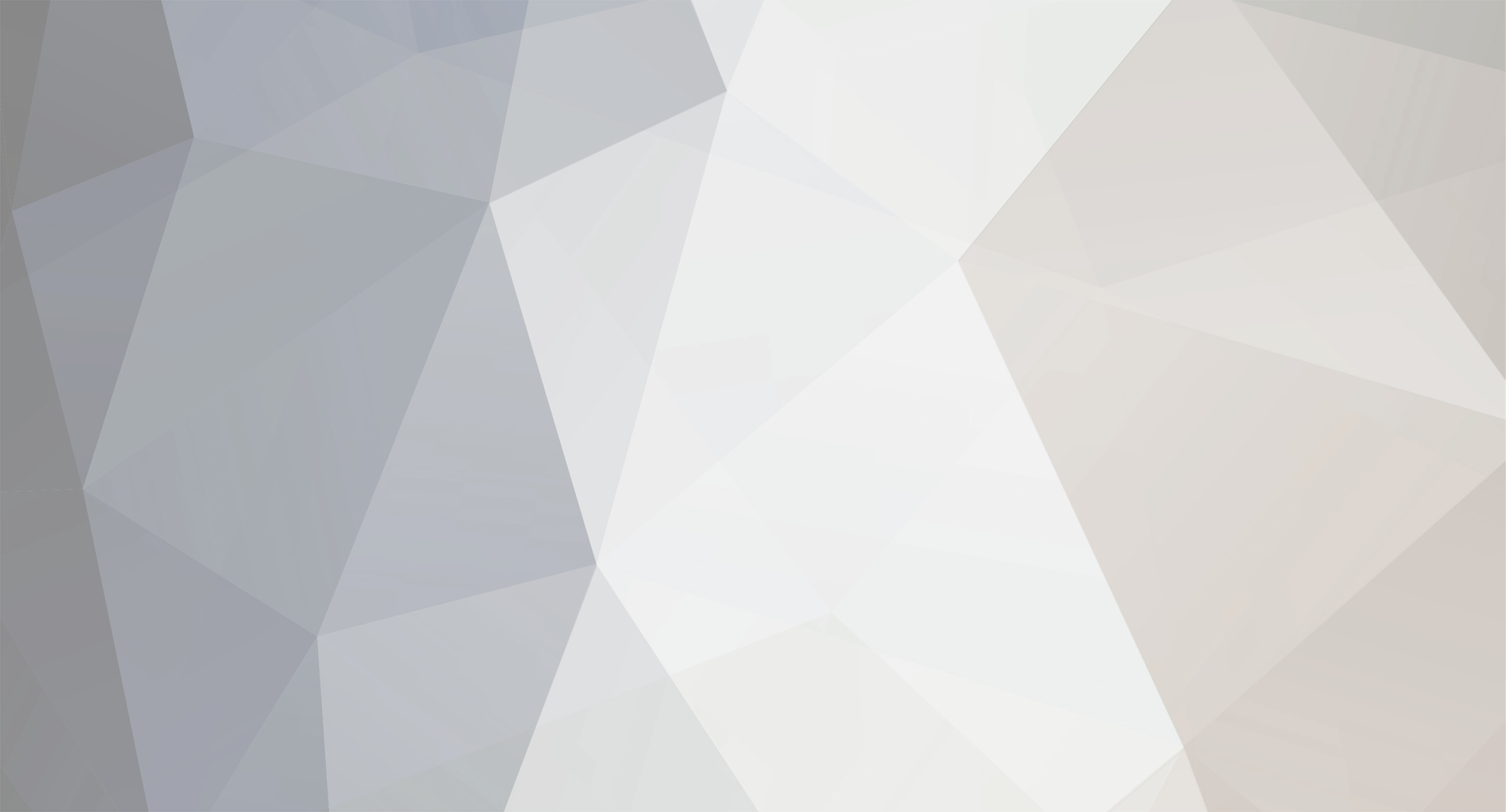
John Olsen 1
Members-
Posts
469 -
Joined
-
Last visited
Never
Content Type
Profiles
Forums
Blogs
Gallery
Calendar
Downloads
Everything posted by John Olsen 1
-
Even Experienced Modellers Can Make Beginners' Mistakes.
John Olsen 1 replied to David Davis's topic in Incident Reports
I've had the fin fall off on a Great Planes 40 size Stik. The root cause is that the bottom edge of the fin that goes into the fuselage has the grain running fore and aft, so that the balsa is being stressed across grain. The bits of vertical grain on the leading and training edge don't engage significantly with the slot in the fuselage, so it is very weak...but not obviously so unless you are looking at one with all the covering stripped off. They really need some reinforcement in this area, which I have done using bits of kebab stick for dowels. Other than that weakness, they are a good plane and fly well. John -
Just for interest, take a close look at the actual break. Quite often you will find that part of the break is smooth, perhaps with a faint pattern like tree growth rings, while the other part is rough, looking almost crystalline. What happens is that a tiny crack starts, perhaps from a scratch. With each reversal of load, the crack grows a little. With a crankpin, the load reverses every cycle. Eventually the crack is big enough that the rest of the metal fails abruptly, giving the rough break. When the crankpin on my AM15 failed many years ago, that was exactly what the break looked like. It does not help that there is a stress concentration in the corner, and it is kind of hard to design a crankshaft that does not have such a stress concentration, although there is usually a radius there to help with that. But to some degree, if it was strong enough to never break, it would be too heavy. For a given loading, there is a critical crack length, beyond which the crack propagates through the material at the speed of sound, so the final failure is very sudden. Also corrosion will both help such a crack get started, and help it to grow once it has started. On the other hand, if the engine was too lean and did a backfire, it might have managed to put enough stress on the pun to just bust it outright. A crack growing is not exactly the same as fatigue, although the effect is similar. (eg failure after some time in operation.) But metals that are prone to fatigue will fail even without an initiating scratch. The repeated cycles of loading are able to alter the crystal structure so that eventually the piece fails under a much lower load than it could withstand when new. John
-
While the Russians would like to blame the whole thing on the Mirage, the fact remains that the Tupelov broke up in mid air, without having actually collided with anything else. Should an aircraft that can fly at over Mach 1 be structurally weak enough to break up at a much lower speed when manoeuvering? It is now known that much of the airframe was made by milling from large slabs of aluminium, and apparently these were prone to developing cracks. This was one of the reasons that they were eventually withdrawn from service. Milling parts from solid is a process that is used in aircraft, but you have to be able to produce large slabs without flaws. The talk of spying is much over rated. No doubt the Russians did gather as much information as they could, but despite the external similarities, the internal design, particularly the structure, was quite different. The external shape is pretty much determined by the aerodynamics. Even with subsonic designs, all large passenger transports tend to look much the same, apart from earlier experiments with putting engines in different places. Even if they had a full set of drawings, the different production facilities and the different sources of parts would require a major redesign anyway. If you look around on Utube there are some good videos about all this. One of the Russian guys said that they were actually about 15 to 20 years ahead of having the capability to design and build such an aircraft successfully. John
-
ESM do a large scale Dornier 335. I have one, but I have not finished putting it together yet. I also have the little foamy one which goes well, although it is very easy to lose orientation with it. Currently needs some repairs! There were also some German guys producing a kit with a shaft drive to the rear propeller, as per the original, so the rear engine goes in the right place. Good idea so long as the engineering of the shaft is up to the job. The ESM one can either have a single petrol engine up front, or a pair of engines. Mine has a 160 twin up front and a 120 single down the back. Apparently as a model they fly well, without the usual problems associated with warbirds. John
-
Mixing brushless motors, ESCs with water!
John Olsen 1 replied to Delta Foxtrot's topic in General Electric Flight Chat
Actually the ideal shape of a marine prop depends on the speed and torque of the power plant, as well as the available space. Usually boats are quite limited in the diameter that can be accommodated, due to the maximum draft that is acceptable. So to accept the required power, the blade area has to be quite large, and they often have to be run quite fast as well. This leads to cavitation problems, so the blades are kept quite thin. If the space is available, a shape more like an aeroplane propeller will actually give more efficient results. However the speed has to be low enough to keep the tip speed reasonable. One form of power where this applies is with small steam plants. Steam engines usually run quite slow...my own engine is considered a high speed one as it runs up to about 600 rpm. The propeller I need to make for it will be 21 inches diameter and 21 inches pitch, and will look more like an aeroplane propeller than the usual boat type. It will have two blades. Note though that it will only be absorbing about 10 hp, which should, all going well, push the boat along at about 7 or 8 knots. This is actually about as fast as the hull would go, since this is a displacement hull, not a planing one. (The hull is 30 feet long) I think in fact a human powered boat would have similar requirements....the power plant is capable of good torque but only at low rpm. To get the best out of it, you want a large diameter high aspect ratio propeller, turning at low speed. But of course, said propeller must be fully submerged and also must not be touching the bottom of the water, so the maximum diameter may be limited. There isn't enough power to plane, so a long displacement hull will minimise wave drag and give the best performance for the limited power. (that is also why rowing eights are so long.) Even on aircraft, where possible we would use a larger propeller turning at a lower speed if we want high efficiency. However we must often sacrifice efficiency for practical concerns like not having a grasshopper like undercarriage. We can't turn a large propeller fast or the tips will exceed the speed of sound. In order to absorb more power in a limited diameter, we add more blades, although this leads to interference like on a biplane, and so reduces efficiency. John -
XT60 connectors...
John Olsen 1 replied to Tony Harrison 2's topic in Building from Traditional Kits and Plans
While we are talking about XT60, I found recently that Hobbyking is selling a little tool plus some plastic bits that make it much easier to unplug XT60 in a hurry. You install a little U shaped piece of plastic onto the male and female parts of the connector, then when you want to unplug you slip on a little plastic plier device and squeeze it, and it pulls them apart without wrenching on the wiring at either end. Seems quite a good idea to me, although ideally the bit you have to add on should have been part of the connector in the first place. You could of course also do the same sort of thing by drilling holes in a suitable spot in the connector and then using outside circlip pliers to open them apart. John -
I wouldn't have said that big ones are necessarily any harder to make. The parts tend to be larger and less easily damaged in making them. Back in the sixties, when I built my 7 foot wingspan Powerhouse, I noticed that it actually had the same number of wing ribs as the Tomboy model that was then popular with my clubmates. The Powerhouse fuselage was not much more complicated either. It certainly flew better and was much easier to trim. Small changes make a much bigger difference on a small model. With radio control, the small ones tend to be much twitchier as the time constants are much shorter. One effect of the low Reynolds number on small slow aerofoils is that the flow separates much earlier. The result of this is that the aerofoil does not behave anything like the predictions. We used to see turbulators used on free flight duration models, the theory being that it was better to ensure the flow was turbulent, and therefore more predictable, then to try vainly to keep it laminar. But these days we mostly have radio, and if we want a small twitchy model to behave better we can put in a stabiliser to make it behave a little better. I think this is good, since if you are limited in space for building or transport, you can build a smaller model and still have it perform really well. John
-
Restoring a Hobby King Slow Stick
John Olsen 1 replied to Simon Chaddock's topic in Build Blogs and Kit Reviews
I have one of these. It flies quite well although it prefers really calm conditions. Would be fun indoors in a large enough hall. I don't think the electronics would be that critical so you should be able to find something cheap that will do. Mine has been known to drop the undercarriage out in flight, but it flew fine without it. It just relies on the spring of the wire gripping in the slot. I found that I could only easily get a slightly bigger battery than specified, but that worked out fine since the battery is well forward to get the right CoG anyway...no lead needed. John -
Hi again, Try **LINK** You might find it takes a couple of tries to lap a piston to fit the cylinder, but a few extra pistons is not a big deal. I still have a model I built when I was about 14, and it flies again too. I didn't build the engine but I did convert it to spark ignition. John
-
Hi Percy Whereabouts in NZ are you? I could put you in touch with a guy here in Cambridge (NZ) who has built a number of model aero engines and is currently working on a 12 cylinder blown two stroke...I forget the capacity but it is about 8 or so inches long...there is a thread on the Model Engineer website with photos. Anything that he can't tell you about lapping probably doesn't matter. I also know some guys in Auckland who could help out with small quantities of casting sand. Another possibility these days is to draw it up as a 3D model and 3D print the wax...which can be done for you...then have a lost wax casting made. One of the members of the Auckland Model Engineers has been doing this. This gives very high quality castings. John
-
My son has the Balsa USA version of a Taube, in the smaller size. (60 size engine) That one does not have ailerons, while their larger one does. I had some correspondence with them at the time we built it, and they feel that the ailerons are not actually necessary. This seems to be born out by the way it flies, the rudder puts a bank on very effectively. Although it is obviously not an aerobatic aircraft, it is very pleasant to fly. Remember that the full size would not have been doing aileron rolls either! If you want to be really authentic, you could build it with a more scale like structure and include the wing warping. John
-
Hi Tony, That looks quite promising, provided you use it with the correct type of motor...it is quite a different type to the ones here in NZ, but I guess must be common enough over there. You will of course need to pay attention to mechanical and electrical safety if you put together something like that. John
-
Most of the smaller devices that have speed control, like drills, sewing machines etc have universal type motors in them. There is nothing to stop you using a motor of this type, although they might be at the low end of the power range that you want, and not all are meant for continuous operation. A drill for example might not take kindly to being run continuously. Universal motors can be speed controlled with a relatively simple controller. Washing machines are another story....Fisher and Paykel here in NZ pioneered the use of a permanent magnet three phase inverter motor in washing machines. This makes the whole thing a close cousin of the type of thing we are using in model planes these days, but a bit larger. (Not necessarily more powerful!) The earlier motor was similar in appearance to a normal style of mains motor with a belt drive but the later ones are a multipole machine with direct drive to the washing machine drum. They are very popular with the self sufficiency guys as they make an ideal alternator for a windmill to drive, since they can generate at quite a low speed. As a motor, they can run very slow for the washing cycle and very fast for the spin. They would be ideal for what you want except you would still need a VFD, or else enough electronic knowledge to repurpose the inverter from the machine...which would not be easy. You might look out for information on rock tumblers..they are a bit smaller but have similar speed requirements. I wonder myself if just having a couple of pulley sizes on a countershaft would provide enough speed variation. That would allow the use of a simple motor salvaged from a washer or drier. You would have to stop to change speed but I can't see that being too much of a problem. Are the alpacas good eating? I suppose there are quite a lot of neck chops. John
-
So...I had a 40 size Great Planes Stick with a 60 sized electric plant. It went really well until I muffed up the recovery from inverted flight and broke it. So I got another and powered it the same. Then I got to looking at the remains. I rebuilt the smashed wing half, and put a nacelle on each wing and powered it with a pair of 30 sized electric motors. The maiden was really promising, until the rudder and fin failed. I think the sequence was that the rudder split just above the horn, then fluttered until it broke the fin away, just when I nearly had it down. Damage was not too bad and it is nearly ready to try again, this time with improved rudder and fin, which I would say is a bit of a weak point in the original design. The rudder has the grain going the wrong way, and the piece of the fin that glues into the slot in the fuselage also has the grain going long ways, so it is not very strong. Both can easily be improved with a few cocktail sticks glued into holes. I know other people have built twin engined Sticks, so I don't claim originality, but it would be the most radical mod I have done. An overpowered Stick, whether twin or single engine, is a lot of fun to fly. John
-
The usual VFD (Variable Frequency Drive) is meant for three phase motors. They are not too expensive these days but you do need a three phase motor. If you are buying a motor new a three phase one is likely to be no dearer and quite probably cheaper than a single phase one, but of course you are not so likely to be able to salvage one out of an old washing machine. You may be able to get one from the sort of place that sells second hand machine tools or even from a computer scrap outfit. John
-
Taking the FPV plunge...
John Olsen 1 replied to Spice Cat's topic in Aerial Photography, First Person View, UAVs
I recently bought one of the Hobbyking Quanum kits as referred to by others above. I've installed the camera and video transmitter in a Dynam Hawksky, a powered glider a bit like the Bixler. It has been flown a couple of times, so far only using the FPV as a spectator. Seems pretty usable to me, and excellent for the money. I'm waiting until I have a second (control) transmitter available before I try controlling it while on FPV. I want to have the observer as another pilot with a buddy box so he can take over if I get a bit lost, at least for the first few flights. The range seems to be about what they claim. I did have one minor problem to start with, there was a bad solder joint on the lead for the video receiver, which caused it to intermittently stop working. Found that before it went in the air. John -
Douglas XB42 Mixmaster
John Olsen 1 replied to Colin Leighfield's topic in Build Blogs and Kit Reviews
Apart from the planes you have shown at the start of the thread, the Dornier Do335 also had tandem engines for low frontal area. Instead of coaxial propellers at one end or the other, it had one at each end. This led to the use of a cruciform tail unit to protect the rear propeller from ground contact, and a rather tall undercarriage to give enough clearance and to allow rotating for takeoff. The German nickname for it was "Ameisenbar" which means anteater, a very apt description. More officially it was a "Pfeil", which means arrow. There is a German kit for it that uses a shaft to get the power from the rear engine, which is just behind the main wing, to the prop, as per the original. There is also an ESM ARTF kit that either uses a dummy propeller on the back, or alternatively a smaller engine on the back than on the front. The ESM one has been done as an electric model too, but ends up quite heavy by the time you get the CoG right with a heavy battery somewhere down the back. There was also a foamy one a year or two back, with twin outrunners and ESC's from a single 3S lipo. I have one, it goes very well and looks the part, but is very easy to lose orientation on. I also have the ESM one with a 160 twin at the front and a 120 single at the back, but have not finished it yet. John -
Making a LED act like a filament lamp
John Olsen 1 replied to Stevo's topic in Gadgets and Electronics
Maybe I can help clarify how to vary the brightness of an LED. As Dickw's graphs show, the current through an LED will increase quite rapidly with small increases in Voltage. This makes it hard to control the brightness by directly controlling the Voltage across the LED. Adding to the difficulty is the fact that the forward Voltage drop will vary with temperature, so the current will tend to increase as the LED warms up. Because of this it is usual to run LEDs in a constant current mode, or close to it. The simplest way of achieving this is with a series resistor. We decide what current we would like to run the LED at, and calculate a resistor that will give that current at the desired supply Voltage. We usually know the forward Voltage that the LED will typically drop. (This incidently differs with the different colours.) So we can subtract that from the supply Voltage and then use Ohms law to calculate the resistance needed. So what happens if we vary that resistor to vary the brightness? Well, if we go too low in resistance, the current will go too high and the LED will rapidly shuffle off this mortal coil. So we would need to connect a fixed resistor in series with the variable one, so that the resistance can never go too low. This would work but will probably be very non linear and the resistance would have to go very high to put the LED right out. However, if we vary the Voltage applied to the combination of LED and resistor, the current will vary too. If we halve the Voltage, we will roughly halve the current. This will also roughly halve the brightness. It might not actually look like half, because the response of our eyes to light is non linear. Also, I say roughly, because in fact the Forward Voltage drop of the diode will make a difference. If we start from zero Volts, nothing will happen until we reach the threshold Voltage of the diode. Then it will start to turn on, and as we increase the Voltage the current will increase, increasing the brightness. I mentioned that the response of the eye is non linear. If you look through the viewfinder of an SLR camera where you can manually adjust the aperture you can see this. Everytime you close down one stop you are halving the light reaching your eye. eg each step from 2 to 2.8 to 4 to 5.6 to 8 to 11 to 16 is halving the light you see. So in that sequence, by the time you get to f16 you are only getting 1/32 of the light you started with...but you will still be able to see, especially if you give your eye a moment or two to adapt. So even if you arrange to dim an LED by a linear curve, it will still seem to come on suddenly and then not vary by so much towards the top end. John -
Model makes whooshing sound on fly bys
John Olsen 1 replied to Mark Kettle 1's topic in The Video Channel
Is there a joke on board? -
I would also add that speed was important because the faster aircraft can choose to initiate and break off the action. So they have the choice of whether to dogfight or not...hence sayings like "Never try to out turn a Zero". Deigning an aircraft for a wide range of speeds is what makes it really hard. Supersonic aircraft would probably look quite different if they never had to slow down to land. I always enjoy watching the flaps deploy on a passenger jet when landing. What looked like a monolithic wing a few minutes before suddenly turns out to be mostly moveble bits. John
-
Glow plugs will vary in the current they draw, depending on design, eg hot or cold. So a simple resistance to drop the voltage may cause problems if you change to a different plug. But I suspect many power panels do just use a resistance. Note that the resistance of the meter you are using will be affecting the reading you get. The current will quite likely be higher without the meter. If I was using a 12V battery supply for the plug, I would be looking for a glow driver that can accept the 12 Volt input. Most glow drivers are based on a switch mode power supply so will not waste power. Then later if you want a starter as well, the same battery can also be used for that. I have been using a separate glow stick myself, but I use a small sealed lead acid battery for the starter which is quite convenient. Ideally this would be a deep cycle one. This could easily run a glow driver as well as the starter. Such a battery also has enough energy stored to recharge a few smallish (eg 3S 2200mAh or so) Lipos if you run a mixture of power types. John
-
Headlamp change ... take the wheel off of course!
John Olsen 1 replied to avtur's topic in Chit-chat
My memory of the Ford Ka is driving a hired one from Dusseldorf airport to Aachen late one night nearly 15 years ago. It was a clear night, no traffic about so once I was on the autobahn I was able to hold pedal to the metal all the way to the offramp at Aachen. The little car sat at about 160kph on the speedo all the way, just varying a little depending on the slight grades. Ok, I guess the speedo was probably over reading a bit, but she ran flat out for 100 k without blowing up...I thought that was not a bad effort. John -
self adhesive foil versus 2.4ghz reception ?
John Olsen 1 replied to richard cohen's topic in All Things Model Flying
A Faraday cage can be made of any conductive material, and aluminium, while not as good as copper, is a pretty good conductor. Any openings in the cage should be small, less than 1/10 of the wavelength you want to exclude. Any wires entering, for instance to bring in mains power, need to be filtered to prevent unwanted signals getting in. Even a properly designed Faraday cage will allow some signal in, although the attenuation should be pretty high. The cage itself does not actually require to be grounded, although it usually would be for electrical safety. But a flying airframe wrapped in aluminium foil is likely to make quite a good impromptu Faraday cage, which is why I think they make more sensitive receivers intended for such applications. It is better if you can get the antennae outside the foil. Note that often the antennae is a few inches long, it is only the bared piece on the end that really matters. We could make quite a suitable antenna by making a slot in the foil and connecting the feeder to either side in the middle. This is actually done on full size aircraft, the slot being closed with a suitable dielectric like epoxy fibreglass. It is not necessarily strictly true that 2.4GHz only goes in straight lines. It will reflect nicely from metal objects like fences, shed roofs, cars, and so on. This gives rise to multiple signal paths, which leads to a thing called Rayleigh fading....the signal level will flutter up and down. You may have heard this on an FM radio while driving in areas with poor reception. This is one reason why most receivers have two antennae, or even a satellite receiver. The modulation schemes used are also designed to help cope with rapid fading. (fluttering) This sort of thing is why you can get in building coverage with cell phones, even though the concrete is full of steel reinforcing. As for not giving 100%...100% only means that you have met the standard required. It should be possible to attain it, if not necessarily common. I passed a mechanics examination once with 100%. If you perform all the calculations correctly, show all the working, and answer all the long form questions clearly, what else can they do? It does not mean that perfection has been achieved. If I had sat the same subject at the next level up, which would have been university, I would have been unlikely to do anything like as well. John -
These motors and ESC's are designed with the idea that they will turn at a speed that is proportional to the applied voltage. Hence the kV rating. This is of course only an approximation, but is close enough for practical purposes. So if we take the prop right off, current will be minimum. Just enough to make up friction losses. The bigger the prop the more current the motor will take trying to keep up to speed. The speed will actually drop a little with extra load, but not enough to matter. This is completely unlike the behaviour of a glow motor. Someone mentioned a flywheel. You cannot get the motor to run its rated wattage (power) into just a flywheel. It will only take power until it comes up to speed, after which it will only take enough power to make up the friction losses...bearings and windage. So what would I do with the three blade problem? Well, I have a Wattmeter, so I would put the prop on and slowly bring the motor up to speed, watching the current. If it starts to get too high, I would back off quickly. The prop could then be trimmed and balanced and another try made. Eventually the prop will be small enough to allow the motor to run to the maximum current at full throttle. If we extrapolate the increase in current with load as we increase the load, it would follow that at stall the motor would be taking an extremely high current. Actually if you start out stalled, this may not be the case....the ESC will be trying to get the motor started and will not necessarily just dump a really large current into the motor. I suspect it pulses the coils in sequence while watching for the back emf pulses to detect the motor speed. Once things are working, the ESC can tell what the rotor is doing by detecting the generated voltage. It is possible for an overloaded motor to do bad things very quickly. I had one where, as far as I can tell, what happened was that the nosewheel hit a crack in the dry field and pulled the firewall out, pivoting the prop down so it touched the ground. The resulting increase in load caused the ESC to fireball. The plane then coasted to a halt and I ran over and extinguished the blaze by pulling out the battery and blowing out the remaining flames. This all happened quite quickly. The ESC under normal conditions was not exceeding 80% of its rating. So a smaller prop on an IC engine will cause it to rev higher, maybe too high, causing damage. On a leccy motor it will just reduce the power. A larger prop on an IC engine will load it down to a lower speed, make it easier to start, and within reasonable limits do no harm, although power will be reduced. On a electric plant, it will increase the current taken and if you overdo things will cause damage to the ESC So the two behave quite opposite. This is worth bearing in mind if you change from one to the other. (I use both and have no axe to grind.) Wattmeters are quite cheap, and don't require a degree in electrical engineering. Your main aim is to make sure that at full throttle with the plane held static the current does not exceed the rating for the motor and ESC. It is usual to allow some headroom, eg maybe don't exceed 80%. So you would prop for a current of no more than 40 Amps on a 50 Amp ESC. Current will tend to be less in flight since the plane is moving, reducing the angle of attack of the propellor and so reducing the load. plus of course you don't usually fly at full throttle the whole time. John
-
The Hurricane is what I had in mind earlier when I suggested that the plane you have is vastly superior to the plane you would like to have. While there is no doubt that overall the Spitfire is a better performer than the Hurricane, it was only available in relatively small quantities for the BoB and had the Hurricanes not also been around, the outcome might have been different. The Hurricane was easier to produce, not least because it really represented the final development of the earlier Hawker biplane fighters, so not too much change was needed in production methods. Of course when you are in your Me109 and bullets start whistling past, it is probably a bit hard to tell if it is a Hurricane or a Spitfire on your tail, and you will probably assume the worst. If the BoB had been a bit earlier, Britain would have been in dire straits indeed. On the other hand, had it been a few years later the Germans might well have had jet fighters and bombers. One thing is for sure, it is just as well Dowding dug his toes in about sending more squadrons to France. Meanwhile in yesterdays paper here in NZ: "A celebrated WWII hero who saved lives by shooting down flying bombs has died in Auckland aged 93. Squadron leader and Commanding Officier Harvey Nelso Sweetman was surrounded by family when he died on Thursday." I'm not sure if he served in the actual BoB, but he left NZ in 1940 to go to the UK. He was flying Typhoons when he was shooting down the buzz bombs. **LINK** John