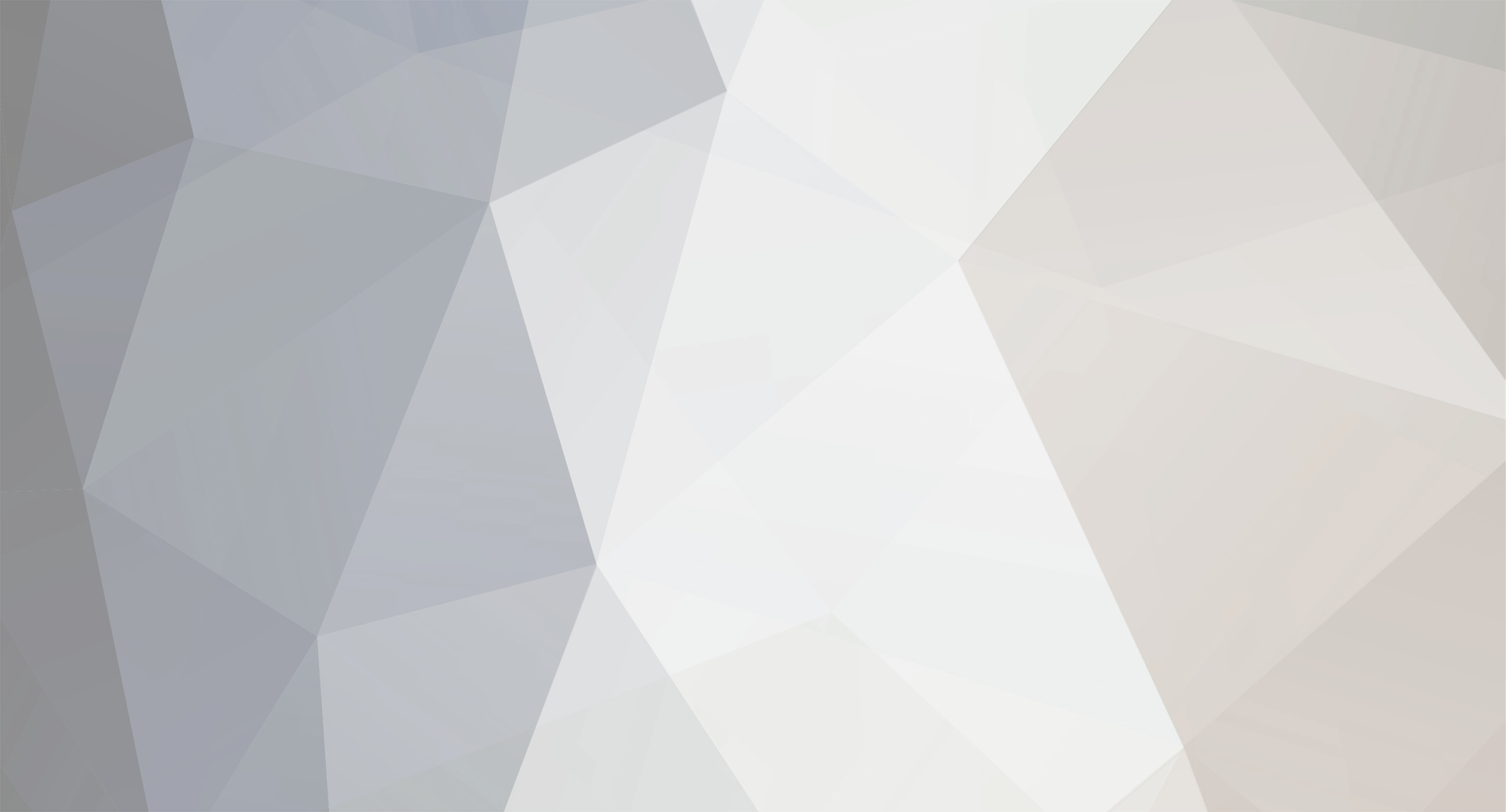
Peter Beeney
Members-
Posts
1,696 -
Joined
-
Last visited
Content Type
Profiles
Forums
Blogs
Gallery
Calendar
Downloads
Everything posted by Peter Beeney
-
Guide to motor selection - suitable power?
Peter Beeney replied to Tony Harrison 2's topic in Motor Discussion
Pat, My first post was simply to try and explain how I might use a tacho to look at how an electric motor was performing and I was just simply stating what I think the wattmeter is measuring. Also I’m not really sure that I said or implied anywhere in the second post that I didn’t know what the meter was actually measuring, sorry if I gave that impression; just an attempt at a friendly answer to your statement. I don’t think I’ll be swapping the tacho anytime soon… Stay cool… PB -
Guide to motor selection - suitable power?
Peter Beeney replied to Tony Harrison 2's topic in Motor Discussion
That’s interesting, Pat, maybe I should do some revision perhaps. My only excuse is that I haven’t got a wattmeter so can I just plead extenuating circumstances…… PB -
Guide to motor selection - suitable power?
Peter Beeney replied to Tony Harrison 2's topic in Motor Discussion
Hi Tony, Another way of trying to find a path through this electrickity maze might be with the help of a tachometer. I’m reluctant about the wattmeter, in my view this is just telling me how many volts and amps are being converted into heat due to the resistance of the power train whereas a tacho will tell me how fast the prop is turning and therefore is an indication of the flying performance of the model. Also by comparing the prop’s speed against the unloaded revs I would get a fair idea as to what the current flow could be. Might be worth a little discussion if this is of any interest at all. PB -
SMS Opto Isolators.
Peter Beeney replied to john stones 1 - Moderator's topic in Gadgets and Electronics
Hi John, I’m not sure if this might be any sort of clue or not, but in the past I’ve been involved in a couple of instances where there has been severe interference from the petrol engine’s CD unit on 2.4. In both cases it was the close proximity of the two batteries, ignition and radio, and in particular the two pairs of cables running partly side by side; when they were separated the interference completely disappeared. Something I’ve not tried but how about a cloaking device, wrapping the batts and cables in tin foil or similar complete with a common connection to a negative; and commoning the two negative poles together at the same time might help too. Of course the simple answer might just be the opto isolator but it did seem to me to be that rather than a signal interruption type of fault it was a power problem caused by the string of inductive bumps on the radio power supply each time the capacitor was being charged up. But that really was purely speculative thinking on my part, we didn’t actually for test any of this. I suspect that like 35MHz PCM radio, any 2.4 radio signal interference would not be able to get into through the radio and into the servos, in the event of total swamping the radio would just stop working and any failsafes activated would operate. Good luck. PB -
Hi James, As with a number of other forumites that have posted here I would agree that your battery state was 99.5% responsible for your crash. An open circuit voltage reading of 4.5 volts for a 5 cell nickel pack says that is well and truly exhausted and under load could not sustain even a light current flow for probably more than just a few seconds. I would give the pack a standard charge, that's 14 - 16 hours at 0.1C and then a discharge test at say 0.25C, nothing too drastic to start with, and if I found I had lost less than about 8% of the capacity I’d just carry on as normal; 8 to 12% needs a little think about and anything beyond about 15% I’d definitely be doing a bit more digging before anymore air time. One small item I’ve not flown without consulting on a regular basis is a LED Receiver Voltage Monitor. This is just a little voltmeter with a scale of probably about one volt and in my experience they are ultra reliable and accurate with it. I’m not really interested in the top end, when I’m in the green carry on up the cavortings as they say, it’s only if I see amber or red would get a bit concerned. I’ve extensively bench tested these in the past, both the nickel and lithium types and I personally think they are impeccable. When I’ve ganged say four together and run up and down the scale with a variable voltage bench supply particularly at the lower end where it really matters they are always perfectly in harmony, most likely to the millivolt… Also it’s worth noting that even if the last red has been lit for a while and the pack voltage has dropped even lower there are still enough watts left in the remaining capacity ‘safety net’ not only to enable a safe landing but a few touch and goes in between as well! Not that expensive either, £2:35 from Hobbyking or £1:81 courtesy of ebay. They can be useful in other ways, too, if the leds run up and down when you waggle the sticks on the ground there is certainly a good chance there could be a problem coming down the track sometime. This is an indication there is possibly a high resistance point in the rx supply circuit somewhere causing a momentary volts drop when the servo motors start up, from wire corrosion to a dodgy connection in a plug and socket, or even the pack itself starting to fail, and is definitely worth sorting before it becomes a rather more obvious ‘black bin bag required, please’ open circuit. Just my take on it all, certainly not intended to be any sort of instructions, but when you watch a large model totally destroy itself at full speed a couple of minutes after take off due to a flat battery very close to where someone is standing in a spot where they have every right to be it does become quite thought provoking…to say the very least… Good luck. PB
-
My first glow motor was a Veco 19 circa 1960, no silencer back then of course but it did have a throttle with a baffle attached that covered the exhaust port when it closed. I was starting to try R/C after control line. A 1.5V plug, I can still remember struggling with the one and half volt dry battery which was not a great success but the lead cell was. So I’ve never seen the need to change really; and indeed if there had been any issues I’d have just added enough silicon diodes in the lead to fix it. I was only just adding to the comprehensive list of ways to light up a glow plug rather than suggesting how others might do it. My little concern with the sockets is that they are not polarised and in special circumstances this can have possible repercussions. It’s early springtime and a modeller decides to check run his model in the garden so he sets it up exactly as he would at the patch complete with the restraint correctly in place. He holds the model steady behind the prop and applies the starter, the four stroke engine, a Saito as I remember, started instantly on a fairly high throttle setting so he instinctively let go and the model shoots backwards before his hand was out of the way.The engine was running backwards. Suffice to say perhaps that the ambulance crew decided on the spot to take him straight to a specialist trauma hospital 15 miles away rather than a new state of the art A&E just five minutes down the road and there they put his hand back together very well, albeit with some loss of feeling in fingers and thumb because of irreparable nerve damage. As he said afterwards, this could have only happened because he’d crossed the starter connections; and because model starter motors have permanent magnets instead of field coils if the input polarity is changed the motor reverses rotation. As I said, undoubtably just a once in a lifetime occurrence; the result of a couple of conditions getting together at the same time. If he’d decided to put just a squirt of fuel in the tank instead of filling it I think it’s unlikely it would have been unable to start backwards anyway. Also I soon realised that although I don’t use a power panel I do use a 12V battery sometimes so I could so easily do the same thing. Perhaps it now may well be the case that my indicator could be a bright red flashing led if I connect the starter motor leads the wrong way round! Stay safe.. PB
-
May I add just another version of a glow driver to the quite varied collection listed within this thread. From just about the time I started tinkering with model engines I’ve always used a 2 volt lead acid cell with an extended lead connected to a glow clip, the schematic for this is very plane and simple, I like very plain and simple. A lead acid because as I remember it’s all I had to hand at the time; back then it was a wet cell; for a long time now it’s been an 8Ah Cyclon cylinder type which does have a nice reserve of capacity. Although I do tend to try and keep it topped up regularly, if lead batteries are discharged and then allowed to stand idle for a while the lead sulphate tends to harden and go high resistance which then can possibly make them difficult to charge. The longer lead also enables the battery to be placed back behind the wing when it’s connected and as I always stand behind the model anyway it’s a simple matter to move it well clear as soon as the engine starts. As regards the indicator situation, in the rare event, so far anyway, that I have to start to wonder if the plug has blown I always have lurking nearby a volts/amps/ohms multimeter which I can connect as an ammeter or perhaps even slightly quicker just as a continuity check. I’ve always thought that many plugs are 2 volt working anyway; in the early days our LMS supplied Fox plugs which were 1.5V but I never had any problems with these either. Also if I may be permitted to go a little off topic for a moment here, I’m a little bit nervous about those 4 mil power output plugs in the power panel and also the power supply batteries within the flight box too. This is loosely aligned with the rule of unexpected consequences and I have seen the outcome of a couple of fairly serious incidents related to these almost forgotten very basic items. Maybe it’s only on a once in a lifetime sort of time scale before anything goes seriously wrong but there has definitely been occurrences of the batteries and chargers causing problems. I think the only concern really is with the 12V 7Ah (or bigger) SLA batteries that folks use in their flight boxes, lithium’s are a different matter. PB
-
Hi Dave, That’s certainly something to give you cause for concern, particularly as you were able to replicate the failsafe operating with a range check but it does make me wonder what exactly is going on there. I’m sure there is absolutely no doubt it’s aerial orientation but could it in fact be an indicator of an overall feeble signal strength as well? I say this because over the years I’ve spent quite a bit of time experimenting with model kit actually trying to make it not work correctly and very much in the main I’ve completely failed. It started back in days of 27MHz and AM CB radio and went on from there. I’ve often tried to get a result with the aerial direction situation but I’ve not succeeded yet; and I’m talking a full length ground range checks, a measured 700 metres. But still LoS of course. Much more than that and I’d definitely fail the eyeball test first so at that point the signal strength wouldn’t matter that much anyway. So what I’m saying here is that I’ve never met a tx - rx combo that didn’t have a 100% hard link together irrespective of wherever their aerials were pointing even at this sort of distance; which is why I’m thinking a 200 yard limit may be a bit suspicious. Maybe worth a little coat of looking at perhaps…… And as an aside, I’ve often seemed to have found that many things aeromodelling on test don’t always behave like convention says they should be behaving…. I even found this happening with the CB radio thingy right back at the start…… Good luck. PB
-
Nik, A pleasure Sir, but I have admit it was but just a simple thought, I’ve never considered it before. A ‘de luxe’ version I might do would be to stagger the cut a sniffer thus ensuring slightly wider wire end separation. I like simple, I find it the easiest way to do anything. Indeed, probably the only way of doing anything these days… Good luck. PB
-
Maybe one way of protecting the battery plug is to cut the socket off a servo extension lead by say an inch, fold the wire back on itself and then make a good job of heat shrinking it all down tight. Use that as a cover when the battery is not in use. Then with perhaps the added precaution of making sure the battery doesn’t ever get involved in a melee in a container particularly with any rough players, very especially metallic types, that should do it for you…
-
Thanks Nik, that now makes good sense of it all. Actually I think you may have got away with it quite lightly perhaps, maybe in some small measure due to the longer lead. In my colleague’s case he’d made two aileron servo extension leads for a glider wing and had somehow put a full short on both. He never would tell me what he’d done but he’d obviously managed to bolt neg and pos quite close to each other somewhere along the line. Without checking anything he put it together and plugged the battery straight into the receiver to try it; and being a nicad it was probably a bit pokey anyway, i. e. a nice low resistance itself as well. Instantly he’d got liquid insulation, well alight, dripping everywhere, mostly on his carpet and for a few moments he said the flames seemed to be springing up around his feet faster than he could stamp them out. Then the wire burnt through and he was just left with some serious explaining to do. When I tried it I found it took a current of around 70 - 80 amps to get this sort of result in these battery sized wires. At 5 volts that’s a total impedance of around 70 down to 60 milli ohms, fairly low I’d have thought. I also read a letter in the BMFA News a long time ago written by someone with a similar story, although his was a short on the rx as I remember. But he’d been tinkering too and he also had the experience of the burning insulation spraying around…. PB
-
Yes indeed, Pat, it certainly looked a bit odd straightaway; I thought at first glance it was a servo lead plug. Not sure of any reason for that third wire unless it had been added later for a specific non standard purpose surely? Also the wires still attached to the pack appear to be in unusually good health too, in my experience of examining these faults in the past the whole length of the wire tends to burn up. A mate nearly burnt his house down shorting a 4 cell rx nicad years ago so I did some experimenting at the time to find out exactly what did go on under these conditions. All in all, something of a little mystery… PB
-
Which side of ESC to mount against model?
Peter Beeney replied to Mitchell Howard's topic in Beginners
Perhaps a slightly alternative way of installing the ESC would be to cut away a piece of the shrink wrap over the heat sink, slightly smaller so that wrap is still held in place around the edges; and then painting the exposed ally with a coat of matt black paint if you have any. Then make sure it’s fully held in the mainstream flow of cooling air. This might be helped by strategically placing baffles to make the cool air flow close to the ESC as opposed to flowing around it. Rather in the manner that similar baffles are placed the cowl of a an i/c engine to make the air flow through the fins rather than around. I don’t think I’ve ever even considered sticking the ESC to anything; seems a little too close to temping providence for me. I’d have thought they generally need all the help they can get to keep that lump on the front in constant good circulation…. Just a thought… PB -
First wattmeter results and subsequent changes
Peter Beeney replied to Mitchell Howard's topic in Beginners
Hi Mitchell, I think I would go along with Matt too, I would have a little play around with it just to find out exactly how it all works. One way of doing that might be like this. Using the nominal voltage of 14.8 for a 4 cell lipo to make a datum line to start from the unloaded speed of the motor is 11,840rpm. I consider for my purposes I want the motor to run with a prop that lets it run in the most efficient way possible, that would be about 20% down from the unloaded speed, so that’s a rather precise 9,472rpm. Your current? (present) set up at a 7 minute run suggests the the average current flow throughout the flight was approx, 37 - 38 amps. All these figures are very general fag packet figures by the way. If by changing prop sizes I could arrive at an average flight current flow of around say 18 -19 amps but with the same flight performance as the 6 - 7 minute flight then that would extend my flying time to something like 12 - 14 minutes. I know that as the prop size gets smaller the motor speeds up and the current flow reduces proportionally so I’d start with a small version and try various sizes ether way until I found the best all-round answer. I think it’s possible that a smaller but faster turning prop may provide almost as much tug as a larger but slower turning one in some cases at least. This is a very brief idea, perhaps a little bit different too and may want some explanations but they are all there. Two small points, your model’s wing loading appears to be 20 oz to the square foot, that’ll do nicely for me and if the 8 inch pitch prop starts turning at 9,472rpm that will give the model a theoretical forward velocity of 70mph………. Enjoy it all… PB -
First wattmeter results and subsequent changes
Peter Beeney replied to Mitchell Howard's topic in Beginners
Hi Mitchell, If it were mine think I would be wanting to just simply put a 10 x 6 ACP i/c prop on and give it check out. I’m not a big fan of E props but I’m probably far too much of a hooligan… My first check is with a tacho, if it’s running at something like about 15% down from the unloaded rpm (which I’ve already checked by the way) and that might be somewhere in the ball park figure of 10,000rpm then I might like to think I’d got a topping trainer. Training models of this nature have flown for many years now using the ubiquitous 10 - 6 or something very similar driven by a good 40 i/c motor with great success and aplomb by many aspiring aviators. The propeller is not going to be the least bit concerned about what is turning it round, it will just get on with it. Then I’d check the current flow which at this level I’m sure is not going to cause any sleepless nights at all, sort the spinner out, probably with a gentle screwdriver adjustment and definitely provide some adequate ventilation. Now I’m soon be going to think a possible test flight. If I’m a beginner this would start with with a proper check on control throws and motor run, ALWAYS but ALWAYS standing BEHIND my well restrained model and then invariably followed by a walk to the strip and hence into the bluey. Very good luck with your model! PB -
Bas, Without knowing very much about your model and it’s power train it’s perhaps a little bit difficult to make any suggestions but as regards slow scale style flying this might just be something of a little pointer. A prop with a 6 inch pitch turning at (say) 8,000rpm will give you a theoretical forward speed in level flight and still air of about 45mph; a 4 inch pitch spinning at 10,000rpm will move forward at approximately 38mph whilst a 3 inch at 11k will only achieve a mere 31 miles to the hour. As said, these are very much ‘roundabout’ figures, there are other little factors always waiting in the wings? (sorry) to come into play, such as ‘prop slip’ and ‘props unloading’ etc.; but I’d try a bit experimenting and a few test flight and it shouldn’t be very long before I’d have a very good idea how the model was going to fly. Or not, maybe…. A bit of a moot point perhaps, but I tend to just use a tacho as my sonic screwdriver, followed by a contact thermometer looking for hotspots if I’m suspicious and sometimes a clip on power meter just to confirm what I’ve estimated the current flow to be. All part of the fun! Good luck with your model! PB
-
It’s getting a bit nostalgic to read about 35 Meg radio nowadays, it’s tending to bring back long distant memories… Aerials are another of those little aeromodelling items that have had their share of comments and discussions here on the forum over the years and I can remember that on one occasion I collected together half a dozen receivers and compared the aerial lengths by lying them side by side. This was just to see how important it was to have exactly the right length, there was a school of thought at the time that suggested it could be very critical, almost to the millimetre. Needless to say, they were all different lengths and there was about 6 inches* difference between the longest and shortest. On a later occasion I was flying a 100 inch powered glider and this had the rx right at the back with the full length aerial hanging out under the rudder. At one stage I noticed that this was considerably shorter than it was supposed to be, by perhaps a bit more than half I should think, and I never did quite understand how that came to be so… also I didn’t have a clue as to how long? it had been like that either, it might well have been a while. After a full distance ground range check I tentatively tried soaring it again and quickly found it made not an iota of difference wherever the model went. Then I though I’d try the inverse state so taking some odd wire from the field box plus the 12 volt iron and in a twinkle an aerial about 6ft long was in perfect working order. Again, neither a single tiny glitch nor a lone tiddly wibble wobble was there ever to be seen in many a jolly jaunt toward yonder cirrocumulus, and I often tended to fly right on the limit of visibility, just to see how far I could get. The set up was a Graupner 600 brushed motor back then, a speed control from one of the very early small electric helicopters, a ‘Whisper’, and 7 and 8 cell nickel packs. The receiver was the Fleet 4 channel miniature one with a MPX crystal and MPX transmitter with a very ducky rubbery MPX aerial. If I’m remembering correctly, Micron advised approximately 39 inches aerial length for their homebuilt rx. I’ve always owned an estate car and always with a second 12 volt battery right at the back permanently connected to the car battery charging system and therefore always charged. I flew in a very convenient private field where I was invariably on my own anyway so I could just sit on the back ledge of the motor and fly. I charged the flight packs by simply connecting them directly to the car battery under the bonnet via the long lead, there was enough resistance to limit the current by an amp or two; the 7 cell packs I disconnected when they got really nice and warm (hot) and an 8 cell could just stay there very slowly simmering anyway, 12 volts are not enough poke to take a 9.6V NiMH pack right up to it’s Delta Peak point; probably at least 13.5V plus required. Still enough charge for a goodly flight, though. NB * Please note the now inevitable revert back to the use of ‘real and proper’ units of measurement in a few days time, will this now be mandatory from 1st Jan or still require a further 4.5 years of debate, d’ya think….. But just as long as a pint is still a pint, looks like a pint and always stays as a pint…….milk, naturally…. All this is just relating my own random experiences of course, merely an observation and definitely not intended to be seen as any form of instruction or recommendation, others may well find that their equipment might respond in a much different manner. PB
-
Hi David, Re. some info. on your ESC. I tried this with some measure of success. Google Art-Tech 60A ESC specification. First hit - Art-Tech 60A ESC | Model Flying (your post) Second hit - Art Tech Controller - RCGroups This opens (Firefox) as a PDF doc. in a user file. Safari opens as an Acrobat Reader Art Tech Controller pdf doc. which is why I think the link won’t work in both cases. Either way, page 2 has the details of their range but is this your ESC? If it is - and I very much suspect it is - then then the whole doc. is an interesting little read, looks like quite a nice piece of kit, I saw an ad somewhere for £31. Looks as bullet proof as most…. Good luck. PB Edited By Peter Beeney on 06/11/2020 23:13:33
-
Hi Roger, I probably wasn’t that far behind you, I’d already guessed that the unloaded revs were in the 17,000 region; 17,285 to be precise. But that in turn is making me more than a trifle suspicious too. Those current consumption figures do tend to stand out from the crowd a little, 52 amps to drive a 9 x 6 on 3S?? Put that lump in your model and you’d flatten the battery in less than three and half minutes! ….And just how far is 52A out of spec. anyway? Can we now barbecue some sausages on the ESC? On the face of it, it appears you are getting an approximate 1,200rpm gain for a 22 ampere current flow increase. Based on this, to get to the sort of figures I might want to be looking at I think I might need to be looking for something like a 7 x 2 prop… Do you by chance have a link to that motor please? I can find the 1,000 and 1,250 ok but not the 1,450. Perhaps it’s gone into hiding, if so is there a reason for this I ask myself? Carry on dabbling, Roger, it’s all getting nicely interesting… PB Edited By Peter Beeney on 05/07/2020 12:15:24 Edited By Peter Beeney on 05/07/2020 12:17:35
-
Just measure the motor revs without a prop on, Roger, that will give you a reliable datum to base all your other measurements on. I usually do it with a 12V car battery, that’s a good constant voltage supply, the load current is minimal; and for the same reason a fully charged 3S is fine, very little voltage sag. Should be a ‘must do’ in every case case anyway. Hope this helps. PB Sorry Pat, you beat me to it… must be late… Edited By Peter Beeney on 04/07/2020 21:42:29 Edited By Peter Beeney on 04/07/2020 21:43:28
-
Yes indeed, you do have a little predicament, Roger, not really many easy answers here I guess. Changing from i/c to electric is not always that simple by the look of it. Just a fag packet type of speculation but if you were starting with a bit more leeway here 2 x 2Ah 4S packs in parallel one behind the other in the fuz might have been an option. That in turn might now make it possible to find the right CoG without any additional weight so it might not be that much heaver anyway. Selecting a prop, to me something like a 10 x 7 looks like a likely first candidate for a fictitious 50in span speedster weighing in at something well under 5lb,(hopefully), that should be turning at least in the order of 10,00rpm. Such that a 40 i/c might do. But 11k would be a bit better, though. Such that a OS MAX-35AX might do. The extra watt minutes we have will allow us to bump up the current to around 35 amps and still have just about 5 mins duration down to 30% capacity. Using nominal figures, an 850 kV motor will spin unloaded at 12580rpm, ideally our prop needs to revolve at about 11000rpm to be within our preset limits, slightly faster would be better. So an 850kV 800 watt motor might be choice. 800 watts still gives us a bit of headroom on the max current flow with fully charged batteries. First setback here maybe a bit of a lack of 850kV’s but a 900 pops up here straightaway which looks to be just about perfect all round for our fag packet…sorry, model. Job done… But if it were only that simple……. With the greatest possible respect all round Roger, I have to say I’m a bit suspicious of the 11/6 at 8500rpm though. As usual I may be completely wrong but that seems to me to be now lurking marginally beyond the borderline of a rather marginal place to be in the first instance! Take care. PB
-
Many thanks in turn for your reply Roger, much appreciated. And at the same time I’d also tend to think that your ability to be able to consistently fly a somewhat underpowered and at the same time rather portly model regularly and safely must be a honest and lasting tribute to your model flying skills too… Being naturally a bit lazy I’ve always picked up the tacho first, at least I can very nearly understand this particular device! When tinkering with a new electric motor I alway check the unloaded revs first, then bolt on a likely looking prop and check again; then in a trice it’s possible to be able to predict to within a reasonable degree of accuracy as to how it’s going to perform and how close (or not!) I am to arriving at the ideal prop size. Of course an added look at the current flow with a clip on power meter and a temperature check for local hot spots with a contact thermometer is never a waste of time either and makes it all a little more interesting anyway; also it might help to find out how wrong, or perhaps not quite so wrong, my guesstimates were in the first instance. Although a slightly more difficult decision to make before you even begin this caper though, is maybe choosing what size of propeller to use for a particular model and also how fast it has to turn to get the result you want… Anyway, all best wishes for a future long and unbroken life for your model… PB
-
So to try and answer your original question, Roger, is that I at least would consider whilst the 10/6 won’t really do much harm it might not make that much of improvement either. Giving it a spin is perhaps the best way to find out; I might be completely wrong, it has happens more than once or three times; but your static figures do suggest that it won’t be quite as efficient. I’m pretty sure that the mechanical turning power at the prop shaft is just about as close as it can be to equalling the electrical power flowing from the battery using the smaller 9 x 6. Also your post describing the battery capacity flying time and discharge calculations now makes it all much clearer. That’s much better! I’d had another look a it and it really didn’t add up very well at all (for me). I was beginning to think there must be something seriously wrong with your 9/6 prop! Having now said all this it seems the model might well have been designed as a pylon racer. If so then it would have been the heavy hammer all the way and then some, no quarter given. Success was going as fast as possible… So with that in mind I now think that you may be flying just outside the border line of some sort of rather ‘unusual’ flight envelope; but you’re obviously very successful with it and it’s exactly what you are wishing to do as well. So all power to your elbow! Or perhaps that that should be stick finger! Many more happy landings. PB
-
Hi Roger, From the motor performance figures you’ve quoted it seems (to me, anyway!) that the 9 x 6 is just about the optimum size you can use. It would appear to be turning at about the best possible point on the output curve. Certainly worth a try with the 10/6 but your figures for that are already suggesting a slight reduction in performance. The increased current flow immediately points to a reduced prop speed which you point out anyway, so slightly less forward speed (performance?) and it will also slightly reduce the battery duration too. So slightly less flying time per charge; and to say nothing of the slightly increased heating effect as well. Another point to make here, but again OIMHO, your 5 minute flying time points to a constant 33A discharge with a 3Ah capacity. Or in other words, more or less constant full throttle use. Might just take a bit of careful thought as how you can improve this, a different, i.e. more powerful motor perhaps, or as suggested, 4 cells. Here you would now definitely have to go down in prop size but if by some magical coincidence you found that trying say an 8 x 5 resulted in around a 26A current flow using a 2.2Ah 4 cell the increased performance might well give you the ability to use less full throttle, (max current flow), so even more flying time. So 27 - 28 amps might be a suitable starting point. Some experimentation might be called for… Although to be quite honest and weighting it all up perhaps the more powerful motor option might really be a better bet. To improve the performance somewhat I’d guess you just need a bit more of the right sort of poke! Re the prop unloading, I think this must happen to all props anyway. It occurs at S&L; and a bit more going downhill but it’s mostly disappeared when you’re climbing; just when you could do with a little help, maybe. Please don’t consider this as any sort of criticism, or indeed any form or instruction on how to do it. It’s just interesting stuff and it’s only just the way I think about and consider it all. I can really understand your motive about flying the model too, I had something of a very vaguely similar experience once, but I’ve not managed to finish the model off yet… Very good luck with it all… PB
-
Motor stutters near full throttle
Peter Beeney replied to Richard Hayward 6's topic in General Electric Flight Chat
Richard, Does a clue now lie in the fact you have 1350 watts versus 860 watts? It did strike me in the beginning that 25 amps at three quarter throttle on the 13 x 8 prop seemed a bit unusual. Plus the fact that the prop seemed to be the only common link during all your trials and tribulations. I always clock the prop speed with a tacho first anyway, that’s a fairly sure way of seeing what’s going on; for me anyway. And my idle thoughts about a warbird of around 9lbs in weight would be that it would surely appreciate at least 1200 watts of power (or just a little bit more, perhaos...) to fly in that nicely spirited manner that warbird should be flown. Flat out! But that’s only my idea, every one has his own personal choices and ideas. Agreeing with Colin it certainly sounds like the Quantum is a potential contender as a replacement. How would you consider your Spit compares physically with your Acrowot? If more or less the same then a likewise power plant might not be far of the button… I’d have thought that the flying characteristics are perhaps not that much too dissimilar, either… Good luck with what ever you try. PB Edited By Peter Beeney on 14/03/2020 19:58:17 Edited By Peter Beeney on 14/03/2020 19:59:16